سیل مکانیکی چیست؟
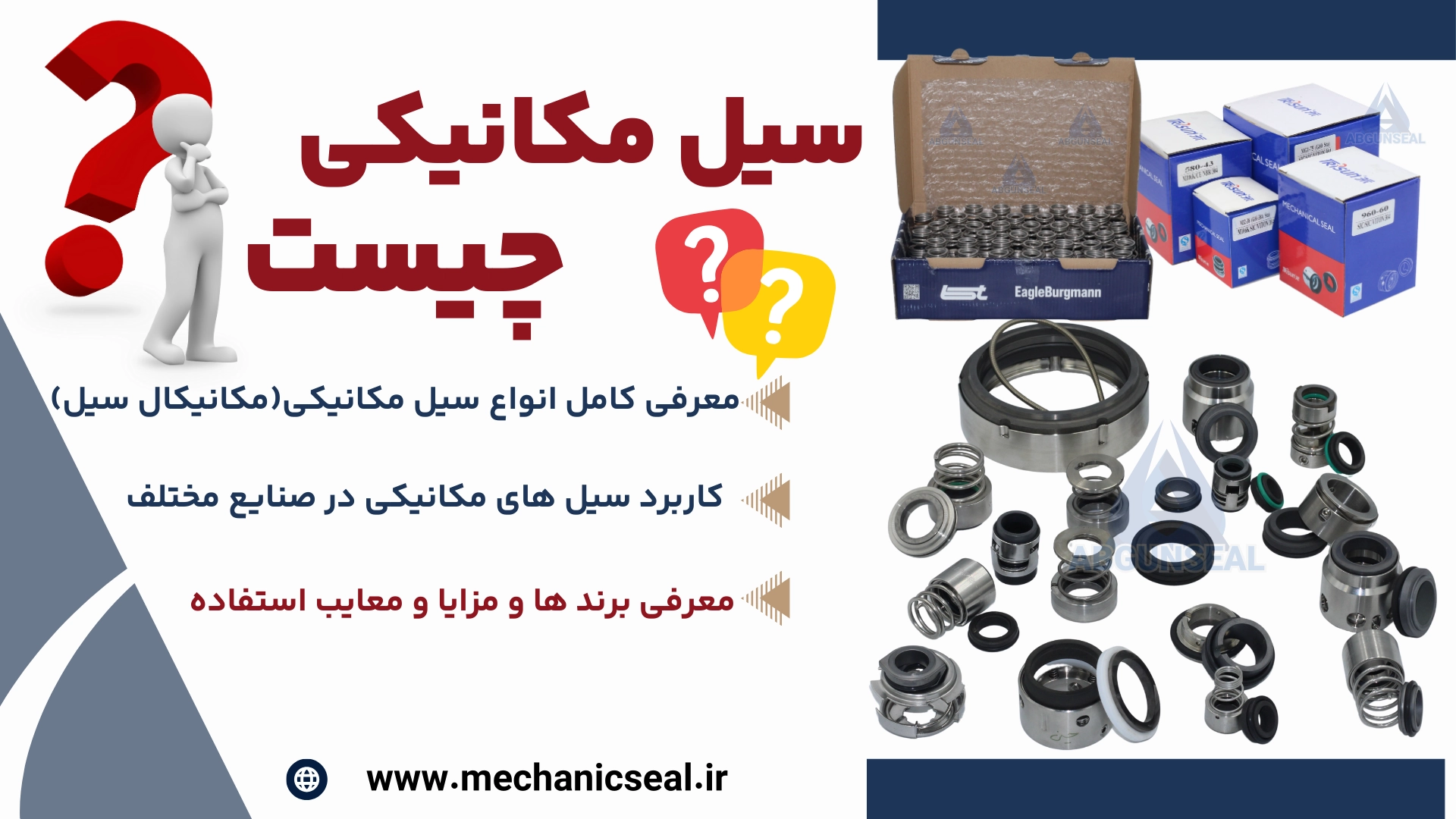
سیل مکانیکی (آب بند مکانیکی) چیست؟ راهنمای کامل
مقدمه: اهمیت آببندی در تجهیزات صنعتی
در قلب بسیاری از فرآیندهای صنعتی، تجهیزات دوار مانند پمپها، میکسرها، کمپرسورها و توربینها قرار دارند. چالشی اساسی در طراحی و بهرهبرداری از این تجهیزات، جلوگیری از نشت سیال (مایع یا گاز) از محلی است که یک شفت دوار از درون یک محفظه ثابت عبور میکند. نشت سیال نه تنها منجر به هدر رفتن مواد ارزشمند یا خطرناک میشود، بلکه میتواند باعث آلودگی محیط زیست، کاهش راندمان تجهیزات، آسیب به یاتاقانها و سایر اجزا، و ایجاد خطرات ایمنی گردد.
در گذشته، روشهای سنتی مانند استفاده از پکینگها (نخهای گرافیتی یا آببندهای فشاری) برای آببندی شفتها رایج بود. با این حال، پکینگها معایب ذاتی متعددی دارند. آنها برای عملکرد صحیح و خنک ماندن، به مقدار مشخصی نشتی کنترلشده نیاز دارند که این امر در مورد سیالات گرانقیمت یا خطرناک مطلوب نیست. اصطکاک قابل توجه بین پکینگ و شفت، منجر به اتلاف انرژی، تولید گرما و سایش شفت یا بوش محافظ آن میشود. علاوه بر این، پکینگها نیاز به تنظیمات و نگهداری دورهای دارند و برای کاربردهای با فشار بالا، سرعت دورانی بالا یا شرایط خلاء مناسب نیستند.
پادکست معرفی سیل مکانیکی
برای سهولت کار شما عزیزان در طول 8 دقیقه یک پادکست کامل برای پاسخ کامل و راحت به پرسش “سیل مکانیکی چیست؟” آماده کردیم که میتوانید گوش کنید و به هر آنچه راجع به عملکرد دقیق این سیل باید بدانید به راحتی دست پیدا کنید.
نام های رایج سیل های مکانیکی
با پیشرفت فناوری و افزایش الزامات صنایع برای کارایی بالاتر، ایمنی بیشتر و حفاظت بهتر از محیط زیست، نیاز به راهکارهای آببندی مؤثرتر احساس شد. این نیاز منجر به توسعه و استفاده گسترده از سیل مکانیکی (Mechanical Seal) یا مکانیکال سیل گردید. این قطعه که گاهی با عنوان آب بند مکانیکی یا به طور خاص در کاربرد پمپها، سیل پمپ نیز شناخته میشود، به عنوان راهحلی مدرن و کارآمد برای ایجاد یک مهر و موم پمپ (یا سایر تجهیزات دوار) قابل اطمینان مطرح شد. سیلهای مکانیکی با کاهش چشمگیر نشتی، افزایش طول عمر تجهیزات، کاهش هزینههای نگهداری و امکان کار در شرایط عملیاتی سختتر، انقلابی در صنعت آببندی ایجاد کردند. امروزه، سیلهای مکانیکی نقشی حیاتی در قابلیت اطمینان، ایمنی و کارایی طیف وسیعی از صنایع، از نفت و گاز و پتروشیمی گرفته تا صنایع غذایی و دارویی، ایفا میکنند. درک عملکرد، اجزا و انواع این قطعات برای مهندسان، تکنسینها و متخصصان نگهداری و تعمیرات ضروری است.
تعریف دقیق سیل مکانیکی و هدف اصلی آن
سیل مکانیکی، مکانیکال سیل یا آب بند مکانیکی، وسیلهای دقیق و مهندسیشده است که برای جلوگیری مؤثر از نشت سیال (مایعات، گازها یا حتی جامدات ریز معلق) از فضای بین یک شفت در حال چرخش و محفظه ثابت اطراف آن طراحی شده است. هدف اصلی این قطعه، ایجاد یک آببندی دینامیکی است که نشتی سیال تحت فشار را به حداقل ممکن، و در شرایط ایدهآل، به سطح نامرئی (بخار) کاهش دهد.
برخلاف پکینگها که آببندی را از طریق فشردن مواد نرم به دور شفت انجام میدهند، اساس کار سیل مکانیکی بر وجود دو سطح (صفحه) آببندی اولیه بسیار صاف و صیقلی استوار است. یکی از این سطوح (معمولاً به نام سطح دوار یا متحرک) به شفت متصل شده و همراه با آن میچرخد، در حالی که سطح دیگر (معمولاً به نام سطح ثابت یا نشیمنگاه) در بدنه یا محفظه پمپ (یا تجهیز دیگر) به صورت ثابت نصب میشود. این دو سطح با دقت فوقالعادهای پرداخت (لپینگ) شدهاند تا صافی سطحی در حد میکرون (معمولاً کمتر از 0.001 میلیمتر) داشته باشند. این دقت بالا در ساخت سطوح، عنصر کلیدی در فناوری سیل مکانیکی است که آن را از روشهای آببندی دیگر متمایز میکند.
اگرچه هدف اصلی به حداقل رساندن نشتی است، درک این نکته ضروری است که مقدار بسیار کمی از سیال فرآیندی، به صورت یک فیلم نازک، بین این دو سطح آببندی نفوذ میکند. این فیلم سیال برای عملکرد صحیح سیل حیاتی است و وظیفه روانکاری و خنککاری سطوح را بر عهده دارد. نشتی واقعی از سیل مکانیکی، در واقع تبخیر همین فیلم نازک سیال در لبه خارجی سطوح و در تماس با اتمسفر است. این میزان نشتی معمولاً به قدری کم است (در حد چند قطره در روز یا حتی کمتر، که به صورت بخار ظاهر میشود) که عملاً نامرئی تلقی میشود. این تفاوت اساسی با پکینگهاست که برای عملکرد به نشتی مایع قابل مشاهده نیاز دارند.
سیلهای مکانیکی فقط به پمپها محدود نمیشوند و در طیف وسیعی از تجهیزات دوار دیگر مانند میکسرها، همزنها، کمپرسورها و راکتورها نیز کاربرد دارند. در تمامی این کاربردها، هدف یکسان است: جلوگیری مؤثر از نشت سیال در نقطه عبور شفت دوار از محفظه ثابت.
نحوه عملکرد آب بند مکانیکی: علم پشت آببندی
عملکرد یک سیل مکانیکی بر اساس یک تعادل دقیق بین نیروها و ایجاد یک فیلم سیال کنترلشده بین سطوح آببندی اولیه استوار است. درک این مکانیزم برای بهرهبرداری صحیح و عیبیابی این قطعات حیاتی است.
آببندی اولیه توسط دو سطح بسیار صاف و صیقلی (یکی ثابت و دیگری دوار) انجام میشود که عمود بر محور شفت قرار گرفتهاند. این دو سطح توسط مجموعهای از نیروهای بسته شدن (Closing Forces) به سمت یکدیگر فشرده میشوند. این نیروها شامل نیروی مکانیکی اعمالشده توسط فنر(ها) و نیروی هیدرولیکی ناشی از فشار سیال فرآیندی است که بر پشت سطوح آببندی اثر میگذارد. فنر(ها) تضمین میکنند که سطوح حتی در زمان راهاندازی یا در شرایط فشار پایین نیز در تماس باقی بمانند.
هنگامی که شفت شروع به چرخش میکند و سیستم تحت فشار قرار میگیرد، فشار سیال باعث میشود مقدار بسیار کمی از آن به فضای میکروسکوپی بین دو سطح آببندی نفوذ کند و یک “فیلم سیال” (Fluid Film) تشکیل دهد. ضخامت این فیلم معمولاً در حد یک میکرومتر (0.001 میلیمتر) است. این فیلم سیال نقشی حیاتی و دوگانه ایفا میکند:
- روانکاری: از تماس مستقیم و خشک بین سطوح دوار و ثابت جلوگیری کرده و اصطکاک را به حداقل میرساند. بدون این روانکاری، اصطکاک باعث تولید گرمای شدید، سایش سریع و تخریب سطوح آببندی میشود.
- خنککاری: گرمای ناشی از اصطکاک (هرچند کم) را جذب و دفع میکند.
همزمان با نفوذ سیال به این شکاف، یک افت فشار در طول مسیر فیلم سیال رخ میدهد، از فشار بالای سیستم در لبه داخلی سطوح (سمت سیال فرآیندی) تا فشار اتمسفر در لبه خارجی سطوح. فشار داخل این فیلم سیال، نیرویی در جهت جدا کردن سطوح (Opening Force) ایجاد میکند که در تقابل با نیروهای بسته شدن عمل میکند.
عملکرد پایدار سیل مکانیکی به حفظ یک تعادل دینامیکی بین نیروهای بسته شدن و نیروهای باز شدن بستگی دارد. این تعادل تضمین میکند که فیلم سیال به اندازه کافی ضخیم باشد تا روانکاری مناسب انجام شود، اما به اندازهای نازک بماند که میزان نشتی (تبخیر فیلم در لبه خارجی) حداقل باشد. تغییر در شرایط عملیاتی مانند فشار، دما (که بر ویسکوزیته سیال تأثیر میگذارد) و سرعت میتواند این تعادل را بر هم زده و بر عملکرد سیل تأثیر بگذارد.
یکی از دلایل اصلی خرابی سیلهای مکانیکی، کارکرد خشک (Dry Running) است. اگر به هر دلیلی (مانند هواگیری ناقص پمپ، سطح پایین سیال در مخزن، یا قطع جریان سیال روانکننده خارجی) فیلم سیال بین سطوح از بین برود، تماس مستقیم سطوح باعث افزایش شدید اصطکاک، دما و سایش شده و در مدت کوتاهی منجر به تخریب کامل سیل میشود.
طراحی سیلهای مکانیکی همچنین به گونهای است که میتوانند انحرافات جزئی شفت، لنگیهای محوری ناشی از تلرانسهای ساخت یاتاقانها و ناهمراستاییهای کوچک را تحمل کرده و آببندی را حفظ کنند. این انعطافپذیری معمولاً توسط فنرها و آببندهای ثانویه الاستومری یا دم فلزی تأمین میشود.
اجزای کلیدی سیل مکانیکی: تشریح “فیبر و فنر“
یک سیل مکانیکی از اجزای مختلفی تشکیل شده است که هر کدام وظیفه مشخصی در عملکرد کلی آببندی دارند. شناخت این اجزا و مواد سازنده آنها برای انتخاب، نصب و نگهداری صحیح سیل ضروری است. اجزای اصلی عبارتند از:
سطوح آببندی اولیه (Primary Sealing Faces / فیسها / کفهها)
این دو جزء، قلب سیل مکانیکی هستند.
- سطح دوار (Rotating Face / کفه متحرک): این سطح معمولاً روی شفت یا یک بوش محافظ شفت نصب میشود و همراه با شفت میچرخد.
- سطح ثابت (Stationary Face / کفه ثابت / نشیمنگاه / Seat): این سطح معمولاً در گلند (Gland Plate) یا محفظه پمپ به صورت ثابت نصب میشود.
این دو سطح با دقت بسیار بالا لپینگ (پرداخت نهایی) شدهاند تا کاملاً صاف و مسطح باشند و بتوانند فیلم سیال نازک را بین خود حفظ کنند. جنس این سطوح بسته به کاربرد (نوع سیال، دما، فشار، وجود ذرات ساینده) انتخاب میشود. مواد رایج عبارتند از:
- کربن-گرافیت (Carbon-Graphite): اغلب برای یکی از سطوح (معمولاً سطح دوار) استفاده میشود. خود-روانکار است و مقاومت شیمیایی خوبی دارد، اما نسبتاً نرم است.
- سرامیک (Ceramic / Alumina Oxide): سخت و مقاوم به سایش و خوردگی در برابر بسیاری از مواد شیمیایی است، اما شکننده است.
- سیلیکون کارباید (Silicon Carbide / SiC): بسیار سخت، مقاوم به سایش و شوک حرارتی عالی، و دارای مقاومت شیمیایی گسترده است. اغلب در کاربردهای سخت و ساینده استفاده میشود.
- تنگستن کارباید (Tungsten Carbide / TC): بسیار سخت و مقاوم به سایش، اما سنگینتر و گرانتر از سیلیکون کارباید است. مقاومت شیمیایی آن به خوبی SiC نیست.
- فولاد ضد زنگ (Stainless Steel): عمدتاً در کاربردهای سبک و برای سطح ثابت استفاده میشود.
آببندهای ثانویه (Secondary Seals)
اینها آببندهای استاتیکی هستند که از نشت سیال در مسیرهای جانبی جلوگیری میکنند: یکی بین سطح دوار و شفت، و دیگری بین سطح ثابت و محفظه پمپ. انواع رایج آببندهای ثانویه عبارتند از:
- اورینگها (O-rings): رایجترین نوع، معمولاً از مواد الاستومری ساخته میشوند.
- گوه PTFE (PTFE Wedge): برای مقاومت شیمیایی بالا و دماهای بالاتر استفاده میشود.
- دمهای لاستیکی یا فلزی (Elastomer or Metal Bellows): در سیلهای نوع غیرفشاری (Non-Pusher) استفاده میشوند و علاوه بر آببندی ثانویه، نقش فنر را نیز ایفا میکنند.
جنس الاستومرهای رایج برای اورینگها و دمهای لاستیکی شامل NBR (مقاوم به روغن، دمای پایین تا متوسط)، EPDM (مقاوم به آب، بخار، مواد شیمیایی ملایم)، Viton® (FKM) (مقاوم به دما و طیف وسیعی از مواد شیمیایی) و PTFE (مقاومت شیمیایی و دمایی بسیار بالا) است. انتخاب ماده مناسب برای آببند ثانویه بسیار مهم است، زیرا محدودیتهای دمایی و شیمیایی این مواد اغلب تعیینکننده محدودیتهای کلی عملکرد سیل است.
مکانیزم اعمال نیرو (Energizing Mechanism / فنر)
معمولاً یک یا چند فنر برای ایجاد نیروی اولیه جهت نگه داشتن سطوح آببندی در تماس با هم، به خصوص در زمان استارت یا فشار پایین، استفاده میشود. انواع مختلفی از فنرها وجود دارد:
- فنر مخروطی تکی (Single Conical Spring): ساده و مقاوم به گرفتگی.
- چند فنره (Multiple Springs): توزیع نیروی یکنواختتر و نیاز به فضای محوری کمتر.
- فنر موجی (Wave Spring): بسیار فشرده.
- دم فلزی (Metal Bellows): هم به عنوان فنر و هم آببند ثانویه عمل میکند.
جنس فنرها معمولاً از فولاد ضد زنگ (مانند SS316) یا آلیاژهای مقاومتر به خوردگی (مانند Hastelloy®) است.
اجزاء داخلی سیل های مکانیکی
شامل اجزای دیگری مانند پوسته (Shell)، گلند (Gland Plate)، بوش (Sleeve)، پینهای محرک (Drive Pins)، پیچهای تنظیم (Set Screws) و نگهدارندهها (Retainers) است که وظیفه نگهداری اجزا در کنار هم، انتقال گشتاور از شفت به سطح دوار و نصب مجموعه سیل بر روی تجهیز را بر عهده دارند.
اصطلاح “فیبر و فنر“
در زبان عامیانه و بین برخی از فعالان صنعت، از اصطلاح “فیبر و فنر” برای اشاره به سیل مکانیکی استفاده میشود. این اصطلاح احتمالاً به دو جزء اصلی و قابل تشخیصتر سیل اشاره دارد:
- “فیبر”: به احتمال زیاد به یکی از سطوح آببندی اولیه، به خصوص سطحی که از جنس کربن-گرافیت ساخته شده، اشاره دارد که ظاهری شبیه به فیبر دارد.
- “فنر”: به مکانیزم فنری قابل مشاهده که نیروی فشاری را اعمال میکند، اشاره دارد.
اگرچه این اصطلاح از نظر فنی دقیق نیست و تمام اجزای پیچیده سیل را پوشش نمیدهد، اما به عنوان یک نام رایج برای مجموعه آببندی مکانیکی به کار میرود و نشاندهنده تمرکز بر اجزای اصلی درگیر در آببندی و اعمال نیرو است.
جدول مواد رایج برای اجزای سیل مکانیکی و مقاومت آنها
جزء | ماده رایج | محدوده دمای معمول (°C) | مقاومت شیمیایی عمومی | مقاومت به سایش |
---|---|---|---|---|
سطح آببندی | کربن-گرافیت (Carbon) | -40 تا 260 (بسته به گرید) | خوب (آب، روغن، حلالها، اسید/باز ضعیف) | متوسط |
سرامیک (Alumina 99.5%) | تا 150 | عالی (اکثر مواد شیمیایی بجز اسید/باز قوی) | خوب | |
سیلیکون کارباید (SiC) | تا 400 (بسته به نوع) | عالی (اکثر مواد شیمیایی) | عالی | |
تنگستن کارباید (TC) | تا 250 (با بایندر نیکل) | خوب (مقاومت کمتر به برخی اسیدها نسبت به SiC) | عالی | |
آببند ثانویه | NBR (Nitrile) | -40 تا 100 (گاهی 120) | خوب (روغنها، سوختها، آب) | – |
EPDM | -50 تا 150 | خوب (آب، بخار، گلایکولها، اسید/باز ضعیف) | – | |
Viton® (FKM) | -20 تا 200 (گاهی 230) | عالی (روغنها، سوختها، اسیدها، حلالها) | – | |
PTFE (Teflon®) | -200 تا 260 | عالی (تقریباً تمام مواد شیمیایی) | – | |
Kalrez® (FFKM) | -20 تا 315 | عالی (مشابه PTFE با خواص الاستومری بهتر) | – | |
فنر و سختافزار | فولاد ضد زنگ 316 (SS316) | تا 300 | خوب (مقاومت عمومی خوب) | – |
Hastelloy® C | تا 400+ | عالی (مقاومت عالی به خوردگی در محیطهای سخت) | – |
توجه: محدودههای دما و مقاومت شیمیایی تقریبی هستند و به گرید خاص ماده، غلظت و ترکیب سیال بستگی دارند. همیشه باید با دیتاشیت سازنده یا متخصص مشورت شود.
انواع متداول سیلهای مکانیکی
سیلهای مکانیکی در طرحها و پیکربندیهای متنوعی برای پاسخگویی به نیازهای کاربردهای مختلف تولید میشوند. دستهبندی آنها میتواند بر اساس معیارهای مختلفی مانند طراحی داخلی، نحوه نصب یا تعداد مراحل آببندی صورت گیرد. شناخت این انواع به انتخاب صحیح سیل برای شرایط عملیاتی خاص کمک میکند.
دستهبندی بر اساس طراحی داخلی:
- سیلهای فشاری (Pusher Seals): در این نوع سیلها، آببند ثانویه (معمولاً اورینگ یا گوه PTFE) که روی شفت یا بوش قرار دارد، باید به صورت دینامیکی و محوری حرکت کند تا سایش سطوح آببندی اولیه را جبران کرده و تماس آنها را حفظ نماید. این نوع سیل رایجترین و معمولاً ارزانترین طرح است، اما حرکت آببند ثانویه روی شفت میتواند منجر به سایش یا هنگآپ (گیر کردن) آن در حضور ذرات جامد یا رسوبات شود.
- سیلهای غیرفشاری (Non-Pusher Seals): در این طرح، از یک دم (Bellows) فلزی یا الاستومری به عنوان آببند ثانویه و همچنین عنصر فنری استفاده میشود. از آنجایی که دم به صورت استاتیک روی شفت آببندی میشود و نیازی به حرکت محوری آببند ثانویه روی شفت نیست، مشکل هنگآپ از بین میرود. این سیلها برای سیالات حاوی ذرات جامد، سیالات چسبناک یا کاربردهای با دمای بالا (در صورت استفاده از دم فلزی) مناسبتر هستند. سیلهای آکارئونی (Bellows Seal) نمونهای از این نوع هستند.
- سیلهای نامتعادل (Unbalanced Seals): در این طرح سادهتر، فشار هیدرولیکی سیال به طور کامل بر روی سطوح آببندی اثر کرده و نیروی بسته شدن زیادی ایجاد میکند. این امر باعث محدود شدن قابلیت تحمل فشار سیل میشود.
- سیلهای متعادل (Balanced Seals): با تغییر در طراحی هندسی سطوح آببندی (ایجاد پله بر روی شفت یا سطح دوار)، بخشی از نیروی هیدرولیکی خنثی میشود. این کار باعث کاهش بار روی سطوح، کاهش تولید گرما و امکان کار در فشارهای بالاتر میشود. (این مفهوم یک طبقهبندی اساسی است هرچند در منابع به تفصیل شرح داده نشده است).
دستهبندی بر اساس ساختار و نصب:
- سیلهای تک فنره یا چند فنره (Single and Multiple Spring Seals): همانطور که در بخش اجزا ذکر شد، سیلها میتوانند از یک فنر بزرگ (معمولاً مخروطی) یا چندین فنر کوچکتر استفاده کنند. سیلهای تک فنره سادهتر هستند و کمتر مستعد گرفتگی با ذرات جامد میباشند، در حالی که سیلهای چند فنره معمولاً کوتاهتر بوده و نیروی یکنواختتری را روی سطوح اعمال میکنند.
- سیلهای جزئی (Component Seals): در این نوع، اجزای مختلف سیل (سطح دوار، سطح ثابت، فنر، آببندهای ثانویه) به صورت جداگانه عرضه شده و باید توسط کاربر در محل نصب، با دقت تنظیم و مونتاژ شوند. نصب این سیلها نیاز به مهارت و دقت بالایی دارد و احتمال خطای نصب در آنها بیشتر است.
- سیلهای کارتریجی (Cartridge Seals): این سیلها یک مجموعه پیشمونتاژ شده و تست شده در کارخانه هستند که شامل تمام اجزای اصلی (سطوح آببندی، فنرها، آببندهای ثانویه، بوش و گلند) در یک واحد یکپارچه است. نصب سیلهای کارتریجی بسیار سادهتر و سریعتر است، زیرا نیازی به اندازهگیری و تنظیمات دقیق در محل ندارند و احتمال خطای نصب را به شدت کاهش میدهند. این سهولت نصب و افزایش قابلیت اطمینان، باعث گرایش روزافزون صنایع به استفاده از سیلهای کارتریجی شده است، علیرغم اینکه ممکن است هزینه اولیه آنها کمی بیشتر باشد. سیلهای کارتریجی میتوانند به صورت تک مرحلهای (Single Cartridge) یا دو مرحلهای (Double Cartridge) باشند.
دستهبندی بر اساس تعداد مراحل آببندی:
- سیلهای تکی (Single Seals): شامل یک جفت سطح آببندی اولیه هستند و رایجترین نوع مورد استفاده برای اکثر کاربردهای استاندارد میباشند.
- سیلهای دوبل (Double Seals / دبل / دوتایی): این سیستمها شامل دو سیل مکانیکی در یک محفظه هستند که برای افزایش ایمنی و قابلیت اطمینان در کاربردهای خاص استفاده میشوند. این کاربردها شامل موارد زیر است:
- سیالات خطرناک، سمی، قابل اشتعال یا گرانقیمت که نشت آنها به هیچ وجه مجاز نیست.
- سیالات حاوی ذرات ساینده زیاد که میتوانند به سرعت سیل تکی را از بین ببرند.
- سیالاتی که خاصیت روانکاری ضعیفی دارند (مانند گازها یا آب سبک).
- کاربردهایی که نیاز به عمر طولانیتر و قابلیت اطمینان بالاتر دارند.
سیلهای دوبل معمولاً با یک سیال واسطه (Barrier Fluid یا Buffer Fluid) که بین دو سیل قرار میگیرد، کار میکنند. این سیال واسطه میتواند تحت فشاری بالاتر از فشار فرآیند (در آرایش Back-to-Back) یا پایینتر از فشار فرآیند (در آرایش Face-to-Face یا Tandem) باشد و وظیفه روانکاری، خنککاری و جلوگیری از نشت سیال فرآیندی به محیط را بر عهده دارد. وجود سیستمهای پیچیدهتر مانند سیلهای دوبل و سیستمهای جانبی (مانند فلاشینگ که بعداً بحث میشود)، نشان میدهد که سیلهای تکی استاندارد برای تمام شرایط عملیاتی، به خصوص شرایط بسیار سخت یا خطرناک، مناسب نیستند و نیاز به راهحلهای مهندسیشدهتر وجود دارد.
جدول مقایسه ویژگیهای انواع اصلی سیل مکانیکی
نوع سیل | پیچیدگی نصب | هزینه اولیه | تحمل فشار | تحمل دما (نوعی) | تحمل ذرات جامد | نیاز به سیستم جانبی | کاربردهای رایج |
---|---|---|---|---|---|---|---|
جزئی فشاری (Pusher) | بالا | پایین | متوسط | متوسط | ضعیف | اغلب خیر | کاربردهای عمومی، سیالات تمیز |
جزئی غیرفشاری (Bellows) | بالا | متوسط | متوسط | بالا (فلزی) | خوب | اغلب خیر | سیالات چسبناک، دما بالا، حاوی ذرات |
کارتریج تکی (Single) | پایین | متوسط | بالا | بالا | متوسط | گاهی (فلاشینگ) | اکثر کاربردهای صنعتی، نصب آسان، قابلیت اطمینان بالا |
کارتریج دوبل (Double) | متوسط | بالا | بسیار بالا | بالا | عالی | بله (سیال واسطه) | سیالات خطرناک، ساینده، روانکاری ضعیف، اطمینان بالا |
توجه: این جدول یک مقایسه کلی است و ویژگیهای دقیق به طراحی خاص و مواد مورد استفاده بستگی دارد.
مزایای بیشمار استفاده از آب بند مکانیکی
استفاده از سیلهای مکانیکی به جای روشهای آببندی سنتی مانند پکینگها، مزایای متعددی را به همراه دارد که اغلب هزینههای اولیه بالاتر آنها را در طول عمر تجهیزات جبران میکند. این مزایا نه تنها به بهبود عملکرد فنی منجر میشوند، بلکه از نظر اقتصادی، ایمنی و زیستمحیطی نیز حائز اهمیت هستند:
- کاهش چشمگیر نشتی: اصلیترین مزیت سیل مکانیکی، کاهش نشتی به حداقل ممکن (اغلب در حد بخار نامرئی) است. این امر در مقایسه با نشتی کنترلشده و ضروری پکینگها، یک پیشرفت بزرگ محسوب میشود. این ویژگی برای سیالات گرانقیمت، سمی، خورنده، قابل اشتعال، رادیواکتیو یا سایر مواد خطرناک که نشت آنها تبعات جدی اقتصادی، ایمنی یا زیستمحیطی دارد، حیاتی است.
- کاهش اصطکاک و مصرف انرژی: اصطکاک بین سطوح آببندی بسیار صاف در سیل مکانیکی به مراتب کمتر از اصطکاک بین پکینگ و شفت است. این کاهش اصطکاک منجر به کاهش توان مصرفی پمپ یا تجهیز دوار و صرفهجویی در مصرف انرژی میشود.
- کاهش سایش شفت یا بوش: برخلاف پکینگها که به مرور زمان باعث سایش و ایجاد شیار روی شفت یا بوش محافظ آن میشوند، سیلهای مکانیکی مدرن (به خصوص نوع کارتریجی) آسیبی به شفت وارد نمیکنند. این امر هزینههای مربوط به تعمیر یا تعویض شفت و بوش را حذف میکند.
- کاهش هزینههای نگهداری: سیلهای مکانیکی معمولاً عمر مفید طولانیتری نسبت به پکینگها دارند و نیاز به تنظیمات و بازرسیهای مکرر ندارند. اگرچه تعویض سیل مکانیکی ممکن است پیچیدهتر باشد، اما فواصل زمانی بین تعمیرات طولانیتر است و در مجموع هزینههای نگهداری را کاهش میدهد.
- قابلیت کار در شرایط سختتر: سیلهای مکانیکی میتوانند در فشارها، دماها و سرعتهای دورانی بالاتری نسبت به پکینگها کار کنند و برای طیف وسیعتری از کاربردهای صنعتی مناسب هستند.
- محیط کار تمیزتر: به دلیل نشتی بسیار کم، اطراف تجهیزات آببندی شده با سیل مکانیکی تمیزتر باقی میماند و هزینههای مربوط به نظافت و جمعآوری نشتی کاهش مییابد.
- قابلیت آببندی خلاء: سیلهای مکانیکی میتوانند شرایط خلاء را نیز آببندی کنند، در حالی که پکینگها در این شرایط ممکن است باعث نفوذ هوا به داخل سیستم شوند.
- افزایش ایمنی و قابلیت اطمینان: به دلیل کنترل دقیق نشتی و عمر طولانیتر، استفاده از سیلهای مکانیکی منجر به افزایش قابلیت اطمینان کلی تجهیزات و افزایش سطح ایمنی، به خصوص هنگام کار با مواد خطرناک میشود. همچنین، کاهش نشتی میتواند از آسیب به یاتاقانها ناشی از آلودگی روغن روانکاری جلوگیری کند.
در مجموع، این مزایا نشان میدهند که انتخاب سیل مکانیکی یک سرمایهگذاری در جهت بهبود عملکرد، کاهش هزینههای عملیاتی بلندمدت (TCO)، افزایش ایمنی و رعایت الزامات زیستمحیطی است. اهمیت فزاینده مقررات سختگیرانه زیستمحیطی و تمرکز شرکتها بر مسئولیت اجتماعی، نقش سیلهای مکانیکی را به عنوان یک فناوری کلیدی در صنعت مدرن پررنگتر کرده است.
کاربرد گسترده سیل مکانیکی در صنایع مختلف
تطبیقپذیری و کارایی بالای سیلهای مکانیکی باعث شده است تا این قطعات در طیف بسیار وسیعی از صنایع و تجهیزات مورد استفاده قرار گیرند. تقریباً در هر فرآیندی که نیاز به جابجایی یا نگهداری سیالات در تجهیزات دوار وجود دارد، میتوان ردپای سیلهای مکانیکی را یافت. این گستردگی کاربرد، اهمیت حیاتی این فناوری را در صنعت مدرن نشان میدهد.
برخی از صنایع اصلی که به طور گسترده از سیل مکانیکی و آب بند پمپ استفاده میکنند عبارتند از:
- صنایع نفت، گاز و پتروشیمی: پالایشگاهها، مجتمعهای پتروشیمی، خطوط انتقال نفت و گاز، سکوهای دریایی (برای پمپهای فرآیندی، پمپهای انتقال، کمپرسورها).
- صنایع شیمیایی: تولید انواع مواد شیمیایی، اسیدها، بازها، حلالها (برای پمپها، میکسرها، راکتورها).
- نیروگاهها: تولید برق (برای پمپهای تغذیه دیگ بخار، پمپهای خنککننده، پمپهای کندانسور، توربینها).
- صنایع آب و فاضلاب: تصفیهخانههای آب و فاضلاب، ایستگاههای پمپاژ، سیستمهای آبرسانی صنعتی و شهری.
- صنایع غذایی و آشامیدنی: تولید لبنیات، نوشیدنیها، روغنها، مواد غذایی فرآوریشده (برای پمپهای بهداشتی، میکسرها، هموژنایزرها).
- صنایع داروسازی: تولید داروها و مواد اولیه دارویی (برای پمپها و میکسرهای با استاندارد بهداشتی بالا).
- صنایع کاغذ و خمیر کاغذ: فرآوری چوب و تولید کاغذ (برای پمپهای انتقال خمیر، پمپهای آب سفید).
- صنایع معدنی: فرآوری مواد معدنی، انتقال دوغاب (برای پمپهای اسلاری).
- صنایع عمومی: سیستمهای تهویه مطبوع (HVAC)، پمپهای سیرکولاتور شوفاژ و آب گرم مصرفی، پمپهای آتشنشانی، استخرها، ماشینهای ظرفشویی صنعتی و خانگی.
تجهیزات اصلی که در آنها از سیل مکانیکی استفاده میشود شامل موارد زیر است:
- پمپها: به ویژه پمپهای سانتریفیوژ که رایجترین کاربرد سیل مکانیکی است.
- میکسرها و همزنها (Agitators): برای مخلوط کردن مواد در مخازن.
- کمپرسورها: برای فشردهسازی گازها.
- راکتورها: در صنایع شیمیایی و پتروشیمی.
- توربینها: در نیروگاهها.
در بازار ایران، علاوه بر برندهای بینالمللی معتبر مانند بورگمن (Burgmann) که به طور مکرر در منابع به آن اشاره شده است، تلاشهایی برای بومیسازی دانش فنی و تولید داخلی سیلهای مکانیکی نیز صورت گرفته است. این امر نشاندهنده بلوغ بازار و وجود توانمندیهای فنی در داخل کشور برای پاسخگویی به نیازهای صنایع مختلف است.
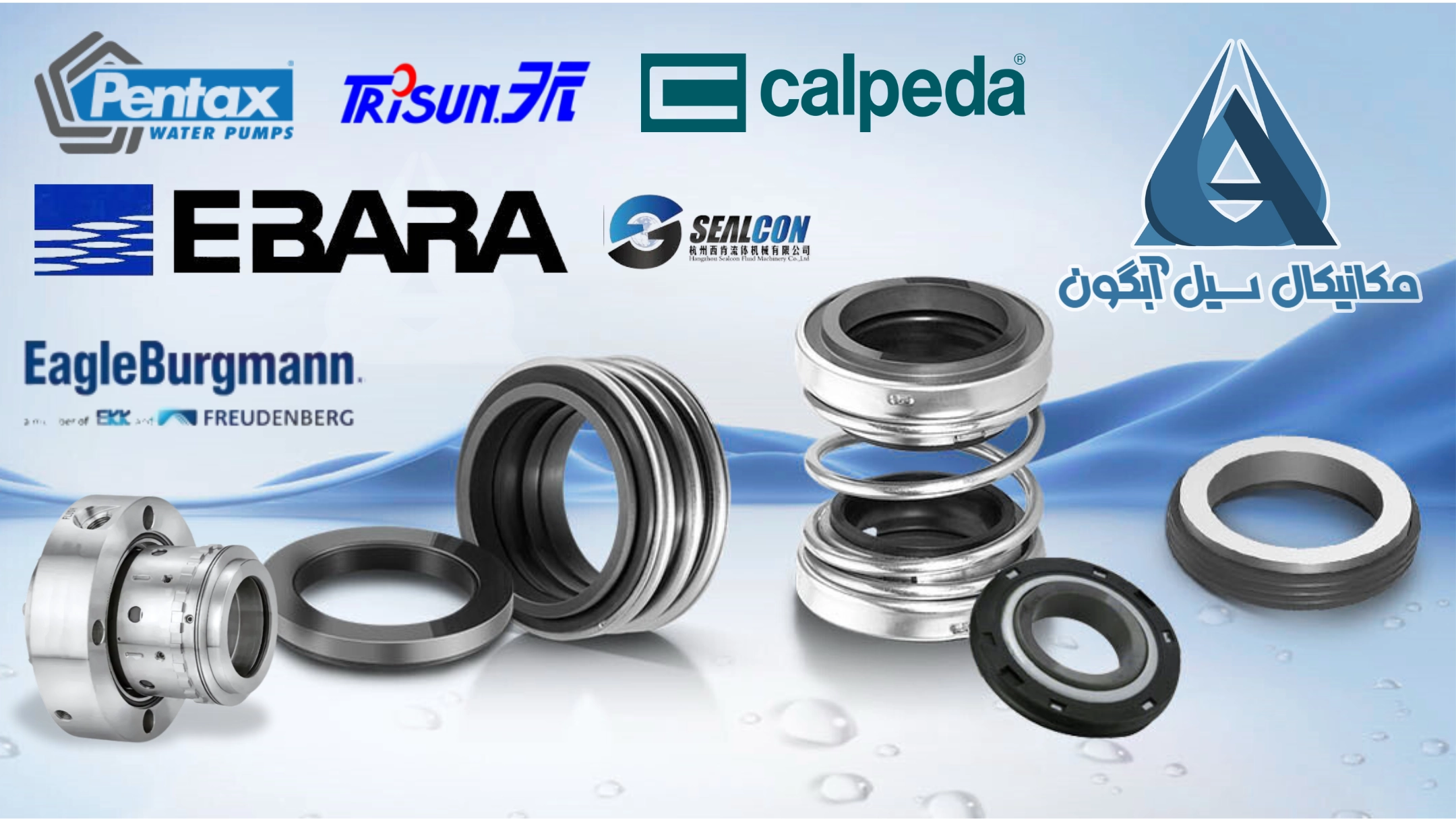
راهنمای انتخاب سیل مکانیکی مناسب
انتخاب صحیح مکانیکال سیل برای یک کاربرد خاص، فرآیندی حیاتی است که تأثیر مستقیمی بر عملکرد، قابلیت اطمینان و طول عمر تجهیزات دارد. انتخاب نادرست میتواند منجر به خرابی زودهنگام سیل، نشتی، توقف تولید و هزینههای قابل توجه تعمیرات شود. این فرآیند نیازمند در نظر گرفتن دقیق پارامترهای متعددی است و اغلب به عنوان یک مسئله بهینهسازی چند متغیره در نظر گرفته میشود که در آن باید بین عوامل مختلف، توازن برقرار کرد. به همین دلیل، در موارد پیچیده، مشورت با متخصصان یا سازندگان سیل اکیداً توصیه میشود ( برای خرید مکانیکال سیل با کارشناسان ما در ارتباط باشید) .
عوامل کلیدی که باید در انتخاب آب بند مکانیکی در نظر گرفته شوند عبارتند از:
- شرایط عملیاتی (Operating Conditions):
- مشخصات سیال (Fluid Properties / Media): این عامل معمولاً مهمترین و پیچیدهترین بخش انتخاب است.
- نوع سیال: مایع است یا گاز؟ آب، روغن، حلال، اسید، باز، دوغاب یا…؟
- سازگاری شیمیایی: آیا سیال با مواد سازنده سیل (سطوح آببندی، آببندهای ثانویه، فنر، قطعات فلزی) سازگار است؟ خورندگی سیال چقدر است؟
- وجود ذرات جامد/ساینده: آیا سیال حاوی ذرات معلق، کریستالها یا مواد ساینده است؟ غلظت و اندازه این ذرات چقدر است؟ سیالات ساینده نیاز به سطوح آببندی بسیار سخت (مانند SiC یا TC) و احتمالاً طرحهای خاص سیل یا سیستمهای فلاشینگ دارند.
- ویسکوزیته: گرانروی سیال بر روی تشکیل فیلم سیال و تولید گرما تأثیر میگذارد.
- سطح pH: میزان اسیدی یا بازی بودن سیال بر انتخاب مواد، به خصوص الاستومرها، تأثیرگذار است.
- کیفیت آب: در مورد آب، پارامترهایی مانند سختی آب اهمیت دارد. آب سخت میتواند باعث ایجاد رسوب (Scaling) بر روی سطوح آببندی شده و عملکرد سیل را مختل کند.
- دما (Temperature): دمای کاری سیال در محفظه آببندی چقدر است؟ دما محدودیت اصلی برای انتخاب مواد آببندهای ثانویه (الاستومرها) است. دماهای بسیار بالا ممکن است نیاز به سیلهای با دم فلزی یا سیستمهای خنککننده داشته باشد.
- فشار (Pressure): فشار داخل محفظه آببندی (Stuffing Box Pressure) چقدر است؟ فشار بالا نیاز به سیلهای متعادل (Balanced) یا سیلهای دوبل دارد.
- سرعت (Speed): سرعت دورانی شفت (RPM) چقدر است؟ سرعت بالا میتواند تولید گرما را افزایش دهد و نیاز به مواد مقاومتر و روانکاری بهتر دارد.
- مشخصات سیال (Fluid Properties / Media): این عامل معمولاً مهمترین و پیچیدهترین بخش انتخاب است.
- طراحی و مواد سیل (Seal Design & Materials): بر اساس شرایط عملیاتی فوق، باید نوع مناسب سیل (فشاری/غیرفشاری، متعادل/نامتعادل، کارتریجی/جزئی، تکی/دوبل) و مواد مناسب برای سطوح آببندی اولیه، آببندهای ثانویه و سایر اجزا انتخاب شود. اغلب یک بدهبستان بین عوامل مختلف وجود دارد؛ به عنوان مثال، ممکن است مادهای مقاومت شیمیایی عالی داشته باشد اما مقاومت به سایش آن کمتر باشد، یا سیل کارتریجی نصب آسانتری داشته باشد اما هزینه اولیه آن بیشتر باشد.
- ابعاد (Size / Dimensions): سیل باید از نظر ابعادی با تجهیزات سازگار باشد. مهمترین پارامترها عبارتند از:
- قطر شفت یا بوش (Shaft Diameter): سیل باید دقیقاً متناسب با قطر شفت در محل نصب باشد.
- فضای موجود: ابعاد محفظه آببندی (Stuffing Box Bore & Depth) باید برای جای دادن سیل انتخابی کافی باشد.
فرآیند انتخاب سیل اغلب با استفاده از حروف اختصاری STAMP خلاصه میشود:
- Size (اندازه)
- Temperature (دما)
- Application (کاربرد – نوع تجهیز، شرایط خاص)
- Media (محیط یا سیال)
- Pressure (فشار)
- (گاهی Speed (سرعت) نیز اضافه میشود)
در نهایت، باید به خاطر داشت که انتخاب سیل بهینه، کلید دستیابی به آببندی مطمئن و طولانیمدت است و صرف هزینه و زمان کافی در این مرحله، از بروز مشکلات و هزینههای بسیار بیشتر در آینده جلوگیری خواهد کرد.(فلوچارت) راهنمای مراحل تصمیمگیری برای انتخاب سیل مکانیکی مناسب
نکات مهم در نصب و نگهداری برای افزایش طول عمر
حتی بهترین و گرانترین سیل مکانیکی نیز اگر به درستی نصب، راهاندازی و نگهداری نشود، نمیتواند عملکرد مطلوبی داشته باشد و به سرعت دچار خرابی خواهد شد. بخش قابل توجهی از خرابیهای سیل مکانیکی ناشی از خطاهای انسانی در مراحل نصب و بهرهبرداری است. رعایت نکات زیر میتواند به طور قابل ملاحظهای طول عمر سیل مکانیکی را افزایش داده و قابلیت اطمینان سیستم را بهبود بخشد:
- نصب صحیح و دقیق:
- تمیزی: قبل از نصب، محفظه آببندی، شفت و تمام اجزای سیل باید کاملاً تمیز و عاری از هرگونه آلودگی، براده، زنگزدگی یا خراش باشند.
- بازرسی: شفت و محفظه از نظر ابعادی، هممحوری، لنگی و صافی سطح بررسی شوند. ناهمترازی یا لنگی بیش از حد مجاز میتواند باعث خرابی سریع سیل شود.
- روانکاری: سطوح شفت و اورینگها (آببندهای ثانویه) باید با روانکار سازگار با سیال فرآیندی و مواد الاستومری، به آرامی آغشته شوند تا از آسیب دیدن آنها حین جا زدن جلوگیری شود.
- دستورالعمل سازنده: نصب باید دقیقاً مطابق با دستورالعملهای سازنده سیل انجام شود. این امر به خصوص برای سیلهای جزئی (Component Seals) که نیاز به تنظیم دقیق طول کاری فنر دارند، حیاتی است.
- مزیت کارتریج: استفاده از سیلهای کارتریجی فرآیند نصب را بسیار سادهتر کرده و احتمال خطای انسانی را کاهش میدهد، زیرا تنظیمات اصلی در کارخانه انجام شده است.
- جابجایی با احتیاط: اجزای سیل، به ویژه سطوح آببندی اولیه که بسیار دقیق و شکننده هستند، باید با نهایت دقت جابجا شوند تا از لبپریدگی، خراش یا ضربه خوردن آنها جلوگیری شود.
- جلوگیری قاطع از کارکرد خشک (Preventing Dry Running):
- این یکی از مهمترین و رایجترین دلایل خرابی سیل است. سطوح آببندی برای روانکاری و خنککاری به فیلم سیال بین خود وابسته هستند.
- هواگیری (Venting): قبل از راهاندازی پمپ، باید اطمینان حاصل شود که محفظه آببندی و کل پمپ به درستی از هوا تخلیه شده و با سیال پر شده است. وجود هوا در محفظه مانع از رسیدن سیال به سطوح آببندی میشود.
- اطمینان از وجود سیال: همیشه باید اطمینان حاصل کرد که سطح سیال در مخزن مکش کافی است و مسیر جریان به سمت سیل باز است.
- سیال واسطه/فلاشینگ: در سیستمهای سیل دوبل یا سیستمهای دارای فلاشینگ خارجی، باید از وجود جریان و فشار مناسب سیال واسطه یا فلاشینگ قبل از استارت اطمینان حاصل کرد.
- تأمین سیال تمیز در سطوح آببندی:
- سیالاتی که حاوی ذرات جامد، ساینده یا تمایل به کریستالیزه شدن دارند، میتوانند به سرعت سطوح آببندی را فرسوده یا مسدود کنند.
- سیستمهای فلاشینگ (Flushing Plans): در چنین مواردی، استفاده از یک سیستم فلاشینگ خارجی یا داخلی برای تزریق یک جریان سیال تمیز و خنک به نزدیکی سطوح آببندی ضروری است. این کار به شستشوی ذرات، خنککاری و روانکاری بهتر کمک میکند. API 682 استانداردهای مختلفی را برای طرحهای فلاشینگ (API Plans) تعریف کرده است. انتخاب طرح مناسب به شرایط فرآیندی بستگی دارد.
- فیلتراسیون: گاهی اوقات میتوان سیال فرآیندی را قبل از رسیدن به محفظه آببندی فیلتر کرد.
- پایش و بازرسی دورهای:
- اگرچه سیلهای مکانیکی نیاز به تنظیمات مداوم ندارند، اما پایش وضعیت آنها میتواند به تشخیص زودهنگام مشکلات کمک کند.
- بررسی نشتی: افزایش ناگهانی یا تدریجی نشتی میتواند نشاندهنده فرسودگی یا آسیب به سیل باشد.
- صدا و لرزش: صداهای غیرعادی یا افزایش لرزش تجهیز میتواند ناشی از مشکلات سیل یا یاتاقانها باشد.
- دما: افزایش دمای محفظه آببندی میتواند نشاندهنده روانکاری نامناسب یا اصطکاک بیش از حد باشد.
رعایت این نکات، اگرچه ممکن است نیازمند صرف زمان و دقت بیشتری باشد، اما در نهایت منجر به افزایش قابل توجه عمر مفید سیل مکانیکی، کاهش توقفهای برنامهریزی نشده و صرفهجویی در هزینههای بلندمدت میشود. در بسیاری از موارد، مدیریت صحیح شرایط عملیاتی و محیط اطراف سیل (مانند تأمین فلاشینگ مناسب) به اندازه خود طراحی سیل در دستیابی به عملکرد مطمئن اهمیت دارد.
نتیجهگیری: چرا سیل مکانیکی یک انتخاب هوشمندانه است؟
سیل مکانیکی یا آب بند مکانیکی، فراتر از یک قطعه صنعتی صرف، یک فناوری کلیدی و راهحلی مهندسیشده برای یکی از چالشهای اساسی در تجهیزات دوار صنعتی، یعنی کنترل نشتی سیالات، محسوب میشود. همانطور که در این مقاله تشریح شد، این قطعات با بهرهگیری از اصول دقیق مهندسی و مواد پیشرفته، عملکردی به مراتب برتر از روشهای سنتی مانند پکینگ ارائه میدهند.
مزایای متعدد استفاده از سیلهای مکانیکی، از جمله کاهش چشمگیر نشتی، افزایش راندمان انرژی، کاهش سایش شفت، طول عمر بالاتر، نیاز کمتر به نگهداری و قابلیت کار در شرایط عملیاتی سختتر، آنها را به انتخابی هوشمندانه برای طیف وسیعی از کاربردها تبدیل کرده است. این مزایا نه تنها منجر به بهبود عملکرد فنی تجهیزات میشوند، بلکه تأثیرات مثبت قابل توجهی بر جنبههای اقتصادی، ایمنی و زیستمحیطی نیز دارند. کاهش هدررفت مواد ارزشمند، صرفهجویی در مصرف انرژی، کاهش هزینههای نگهداری و تعمیرات، جلوگیری از آلودگی محیط زیست و افزایش ایمنی پرسنل، همگی دلایلی هستند که سرمایهگذاری اولیه برای تهیه سیل مکانیکی را توجیهپذیر میکنند.
نقش حیاتی سیلهای مکانیکی در تضمین قابلیت اطمینان فرآیندهای صنعتی مدرن غیرقابل انکار است. خرابی یک سیل میتواند منجر به توقف خط تولید، خسارات مالی هنگفت و حتی بروز حوادث ناگوار شود. بنابراین، درک صحیح عملکرد این قطعات، انتخاب دقیق بر اساس شرایط عملیاتی و رعایت اصول نصب و نگهداری، از اهمیت بالایی برخوردار است.
در نهایت، سیل مکانیکی نمادی از پیشرفت مهندسی در جهت دستیابی به سیستمهایی کارآمدتر، ایمنتر و پایدارتر است. با توجه به مزایای فراوان و نقش کلیدی آن در صنایع مختلف، میتوان گفت که مکانیکال سیل به عنوان راهحل آببندی برتر برای اکثر کاربردهای تجهیزات دوار در دنیای امروز شناخته میشود و انتخاب آن، سرمایهگذاری در قابلیت اطمینان و بهرهوری بلندمدت است.