راهنمای جامع نگهداری سیل مکانیکی:افزایش طول عمر و کارایی
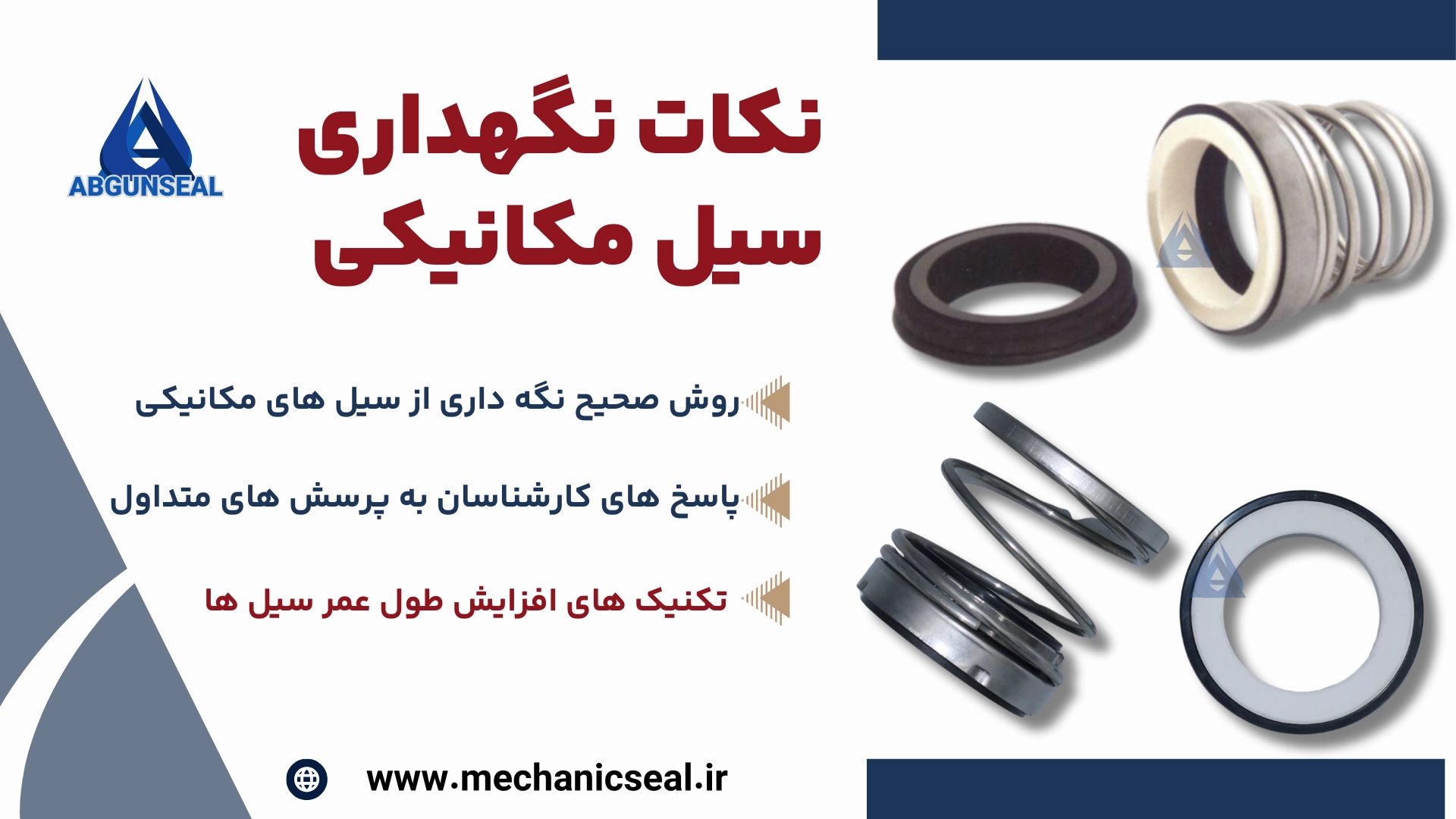
افزایش طول عمر سیل مکانیکی: راهنمای جامع نگهداری و قابلیت اطمینان
مقدمه
نقش حیاتی سیلهای مکانیکی در سیستمهای پمپاژ
سیلهای مکانیکی (آببندهای مکانیکی) اجزای بنیادی در پمپهای سانتریفیوژ و سایر تجهیزات دوار هستند که وظیفه ضروری جلوگیری از نشت سیال در نقطهای که شفت دوار از محفظه ثابت عبور میکند را بر عهده دارند. از زمان کاربرد گسترده آنها در حدود دهه 1950، این سیلها تا حد زیادی جایگزین فناوریهای قدیمیتر مانند پکینگ آببندی (Gland Packing) شدهاند و مزایای قابل توجهی مانند کاهش چشمگیر نشتی (اغلب به صورت بصری قابل تشخیص نیست)، اصطکاک کمتر، کاهش مصرف انرژی، نگهداری کمتر و حذف آسیب به شفت یا غلاف ناشی از پکینگ را ارائه میدهند. سیلهای مکانیکی با مهار مؤثر سیال فرآیندی، برای حفظ یکپارچگی فرآیند، کارایی عملیاتی، ایمنی سیستم و انطباق با الزامات زیستمحیطی، بهویژه هنگام کار با سیالات خطرناک، سمی یا گرانبها، حیاتی هستند.
هزینهها و پیامدهای خرابی سیل
علیرغم اهمیتشان، خرابی سیل مکانیکی یک مشکل مکرر و پرهزینه در بسیاری از محیطهای صنعتی است. اغلب از آنها به عنوان بزرگترین عامل توقف پمپها یاد میشود. هزینههای مستقیم مرتبط با خرابی سیل شامل خرید سیلهای جایگزین (که میتواند از 1000 تا 3000 دلار برای هر اینچ قطر شفت متغیر باشد) و نیروی کار لازم برای جداسازی و نصب است. با این حال، هزینههای غیرمستقیم اغلب این مخارج را تحتالشعاع قرار میدهند و شامل از دست دادن تولید به دلیل توقف تجهیزات، آلودگی احتمالی محصول، هزینههای پاکسازی ناشی از نشت و خطرات قابل توجه ایمنی و زیستمحیطی در صورت انتشار مواد خطرناک میشود. نکته حیاتی این است که درصد بالایی از این خرابیها، که برخی منابع آن را تا 90 درصد تخمین میزنند، پیش از موعد بوده و به دلایلی غیر از رسیدن سیل به پایان عمر طبیعی خود رخ میدهد. این موضوع فرصت قابل توجهی برای بهبود را نشان میدهد.
در حالی که سیلهایی که به خوبی انتخاب شده و به درستی کار میکنند میتوانند به طول عمری بیش از سه سال یا 30,000 ساعت دست یابند، وقوع مکرر خرابیهای زودهنگام نشاندهنده شکافی بین پتانسیل و قابلیت اطمینان واقعی بهدستآمده در عمل است. این تناقض قویاً نشان میدهد که عواملی فراتر از طراحی ذاتی سیل، مانند شرایط سیستم، شیوههای عملیاتی و استراتژیهای نگهداری، اغلب محرکهای غالب خرابی هستند. گذار از پکینگ آببندی سادهتر به سیلهای مکانیکی پیچیدهتر، مزایایی را به همراه داشت اما نیازمند دقت بیشتر و درک عمیقتری از محیط عملیاتی سیل و الزامات نگهداری آن شد.
اهداف راهنما: دستیابی به عمر طولانی سیل از طریق بهترین شیوهها
این راهنما با هدف ارائه یک منبع جامع و تخصصی برای مهندسان نگهداری، مهندسان قابلیت اطمینان، مدیران کارخانه و تکنسینهای ارشد درگیر با تجهیزات دوار تهیه شده است. این راهنما اصول بنیادی مهندسی را با استراتژیهای عملی و کاربردی برای نگهداری، انتخاب، نصب و عیبیابی سیل مکانیکی ترکیب میکند. هدف، پر کردن شکاف بین عمر بالقوه و واقعی سیل با تقویت درک عمیقتر از عملکرد سیل و حالتهای خرابی، و با ترویج شیوههای نگهداری پیشگیرانه و پیشبینانه به جای پاسخهای صرفاً واکنشی است. با اجرای بهترین شیوههای ذکر شده در این راهنما، تأسیسات میتوانند به طور قابل توجهی میانگین زمان بین خرابی (MTBF) سیل مکانیکی را افزایش دهند، هزینههای عملیاتی را کاهش دهند، ایمنی را افزایش بخشند و قابلیت اطمینان کلی کارخانه را بهبود بخشند.
نقش حیاتی سیلهای مکانیکی در سیستمهای پمپاژ
سیلهای مکانیکی (آببندهای مکانیکی) اجزای بنیادی در پمپهای سانتریفیوژ و سایر تجهیزات دوار هستند که وظیفه ضروری جلوگیری از نشت سیال در نقطهای که شفت دوار از محفظه ثابت عبور میکند را بر عهده دارند. از زمان کاربرد گسترده آنها در حدود دهه 1950، این سیلها تا حد زیادی جایگزین فناوریهای قدیمیتر مانند پکینگ آببندی (Gland Packing) شدهاند و مزایای قابل توجهی مانند کاهش چشمگیر نشتی (اغلب به صورت بصری قابل تشخیص نیست)، اصطکاک کمتر، کاهش مصرف انرژی، نگهداری کمتر و حذف آسیب به شفت یا غلاف ناشی از پکینگ را ارائه میدهند. سیلهای مکانیکی با مهار مؤثر سیال فرآیندی، برای حفظ یکپارچگی فرآیند، کارایی عملیاتی، ایمنی سیستم و انطباق با الزامات زیستمحیطی، بهویژه هنگام کار با سیالات خطرناک، سمی یا گرانبها، حیاتی هستند.
هزینهها و پیامدهای خرابی سیل
علیرغم اهمیتشان، خرابی سیل مکانیکی یک مشکل مکرر و پرهزینه در بسیاری از محیطهای صنعتی است. اغلب از آنها به عنوان بزرگترین عامل توقف پمپها یاد میشود. هزینههای مستقیم مرتبط با خرابی سیل شامل خرید سیلهای جایگزین (که میتواند از 1000 تا 3000 دلار برای هر اینچ قطر شفت متغیر باشد) و نیروی کار لازم برای جداسازی و نصب است. با این حال، هزینههای غیرمستقیم اغلب این مخارج را تحتالشعاع قرار میدهند و شامل از دست دادن تولید به دلیل توقف تجهیزات، آلودگی احتمالی محصول، هزینههای پاکسازی ناشی از نشت و خطرات قابل توجه ایمنی و زیستمحیطی در صورت انتشار مواد خطرناک میشود. نکته حیاتی این است که درصد بالایی از این خرابیها، که برخی منابع آن را تا 90 درصد تخمین میزنند، پیش از موعد بوده و به دلایلی غیر از رسیدن سیل به پایان عمر طبیعی خود رخ میدهد. این موضوع فرصت قابل توجهی برای بهبود را نشان میدهد.
در حالی که سیلهایی که به خوبی انتخاب شده و به درستی کار میکنند میتوانند به طول عمری بیش از سه سال یا 30,000 ساعت دست یابند، وقوع مکرر خرابیهای زودهنگام نشاندهنده شکافی بین پتانسیل و قابلیت اطمینان واقعی بهدستآمده در عمل است. این تناقض قویاً نشان میدهد که عواملی فراتر از طراحی ذاتی سیل، مانند شرایط سیستم، شیوههای عملیاتی و استراتژیهای نگهداری، اغلب محرکهای غالب خرابی هستند. گذار از پکینگ آببندی سادهتر به سیلهای مکانیکی پیچیدهتر، مزایایی را به همراه داشت اما نیازمند دقت بیشتر و درک عمیقتری از محیط عملیاتی سیل و الزامات نگهداری آن شد.
اهداف راهنما: دستیابی به عمر طولانی سیل از طریق بهترین شیوهها
این راهنما با هدف ارائه یک منبع جامع و تخصصی برای مهندسان نگهداری، مهندسان قابلیت اطمینان، مدیران کارخانه و تکنسینهای ارشد درگیر با تجهیزات دوار تهیه شده است. این راهنما اصول بنیادی مهندسی را با استراتژیهای عملی و کاربردی برای نگهداری، انتخاب، نصب و عیبیابی سیل مکانیکی ترکیب میکند. هدف، پر کردن شکاف بین عمر بالقوه و واقعی سیل با تقویت درک عمیقتر از عملکرد سیل و حالتهای خرابی، و با ترویج شیوههای نگهداری پیشگیرانه و پیشبینانه به جای پاسخهای صرفاً واکنشی است. با اجرای بهترین شیوههای ذکر شده در این راهنما، تأسیسات میتوانند به طور قابل توجهی میانگین زمان بین خرابی (MTBF) سیل مکانیکی را افزایش دهند، هزینههای عملیاتی را کاهش دهند، ایمنی را افزایش بخشند و قابلیت اطمینان کلی کارخانه را بهبود بخشند.
بخش ۲: عوامل تعیینکننده طول عمر سیل مکانیکی
دستیابی به عمر طولانی مطلوب از یک سیل مکانیکی صرفاً به کیفیت خود سیل بستگی ندارد. عوامل متعددی مربوط به محیط عملیاتی، سیال آببندی شده، وضعیت تجهیزات و شیوههای نصب، عمیقاً بر عملکرد و طول عمر سیل تأثیر میگذارند. درک این عوامل برای نگهداری و عیبیابی مؤثر ضروری است.
تأثیر شرایط عملیاتی
فشار، دما، سرعت و سطوح لرزش خاصی که سیل در حین کار تجربه میکند، عوامل تعیینکننده حیاتی طول عمر آن هستند.
فشار
فشار عملیاتی مستقیماً بر بار روی سطوح سیل، بهویژه در طراحیهای غیربالانس تأثیر میگذارد. فشار بیش از حد میتواند فیلم سیال حیاتی را خارج کرده و منجر به اصطکاک بالا، گرما و سایش سریع شود. همچنین میتواند باعث تغییر شکل اجزای سیل یا اکستروژن عناصر آببندی ثانویه مانند اورینگها، بهویژه در دماهای بالاتر شود. طراحیهای مختلف سیل دارای محدودیتهای فشار مشخصی هستند؛ سیلهای بالانس به طور خاص برای تحمل فشارهای بالاتر با کاهش نیروی بستن هیدرولیکی طراحی شدهاند. علاوه بر این، جهشها یا شوکهای ناگهانی فشار، که میتواند ناشی از رویدادهای عملیاتی مانند بستن ناگهانی شیر تخلیه یا کارکرد پمپ در حالت بسته (Dead-heading) باشد، میتواند باعث جدایش لحظهای سطح، آسیب ضربهای یا تغییر شکل دائمی شده و منجر به نشتی یا خرابی شود. کارکرد سیلها در محدوده فشار طراحی شده و اجتناب از افزایش ناگهانی فشار سیستم بسیار مهم است.
دما
دما بر عملکرد سیل از چند طریق تأثیر میگذارد. بر خواص سیال فرآیندی، بهویژه ویسکوزیته و فشار بخار آن، که برای حفظ فیلم روانکننده حیاتی هستند، تأثیر میگذارد. دماهای بالا تخریب الاستومرهای مورد استفاده برای آببندهای ثانویه را تسریع کرده و باعث سخت شدن، ترک خوردن یا از دست دادن قابلیت آببندی آنها میشود. حتی مواد سطح تماس نیز دارای محدودیتهای دمایی هستند که فراتر از آن خواص آنها کاهش مییابد. گرمای بیش از حد، که عمدتاً توسط اصطکاک بین سطوح سیل تولید میشود، میتواند منجر به تغییر شکل حرارتی سطوح (از دست دادن صافی)، شکست فیلم روانکننده و سایش تسریع شده شود. در خدمات هیدروکربنی، دماهای بالا میتواند باعث کک شدن یا اکسیداسیون سیالی شود که از سطوح نشت میکند و رسوبات سختی تشکیل دهد که در عملکرد سیل اختلال ایجاد کرده و باعث سایش ساینده میشود. برعکس، دماهای بسیار پایین میتواند باعث شکنندگی و از دست دادن انعطافپذیری الاستومرها شود، یا باعث یخ زدن یا جامد شدن سیال فرآیندی شده و منجر به آسیب یا گیر کردن سیل شود. مدیریت مؤثر دما از طریق سیستمهای خنککاری یا انتخاب مواد مناسب حیاتی است.
سرعت (دور در دقیقه شفت / سرعت سطحی)
سرعت نسبی بین سطوح چرخان و ثابت به طور قابل توجهی بر تولید حرارت ناشی از برش ویسکوز در فیلم سیال و اصطکاک تأثیر میگذارد. سرعتهای بالاتر منجر به دماهای بالاتر در فصل مشترک شده و نیاز به خنککاری و روانکاری را افزایش میدهد. برخی طراحیهای سیل، مانند آنهایی که دارای فنر تکی یا پیکربندیهای نصب خارجی هستند، ممکن است به دلیل اعوجاج احتمالی فنر یا اتلاف حرارت ضعیف، محدودیتهایی در حداکثر سرعت عملیاتی داشته باشند. انتخاب مواد نیز نقش دارد، زیرا برخی ترکیبات سطحی در سرعتهای بالاتر گرمای بیشتری تولید کرده یا سریعتر ساییده میشوند.
لرزش و ناهمراستایی
اینها از جمله متداولترین مقصران خرابی زودهنگام سیل هستند. لرزش میتواند از منابع مختلفی ناشی شود، از جمله عدم تعادل اجزای چرخان، ناهمراستایی بین پمپ و محرک، کاویتاسیون، نیروهای هیدرولیکی ناشی از کارکرد پمپ دور از نقطه بهترین راندمان (BEP)، یاتاقانهای فرسوده یا مشکلات رزونانس. ناهمراستایی میتواند استاتیک (قابل اندازهگیری در حالت توقف) یا دینامیکی (رخداده در حین کار) باشد. هم لرزش و هم ناهمراستایی، عملکرد پایدار سطوح سیل را مختل کرده و باعث بارگذاری ناهموار، لرزش سطح و تماس یا جدایش متناوب میشوند. این منجر به سایش تسریع شده و ناهموار سطح، لبپریدگی یا شکستگی مواد شکننده سطح، آسیب فرتینگ به آببندهای ثانویه و سطح شفت/غلاف، خرابی خستگی فنرها یا بلوزهای فلزی و در نهایت، نشتی بیش از حد میشود. حفظ سطوح پایین لرزش و همراستایی دقیق برای دستیابی به عمر طولانی سیل، غیرقابل اجتناب است.
ویژگیهای سیال فرآیندی
سیالی که آببندی میشود صرفاً یک محیط منفعل نیست؛ بلکه به طور فعال با سیل تعامل دارد، به عنوان روانکننده و خنککننده عمل میکند و در عین حال چالشهای شیمیایی یا فیزیکی بالقوهای را نیز ایجاد میکند.
روانکنندگی
توانایی ذاتی سیال فرآیندی برای روانکاری سطوح سیل بسیار مهم است. سیالات با روانکنندگی خوب (مانند روغنها) به راحتی یک فیلم هیدرودینامیکی پایدار تشکیل میدهند. با این حال، بسیاری از سیالات صنعتی رایج، مانند آب، هیدروکربنهای سبک و حلالها، خواص روانکنندگی ضعیفی دارند. آببندی این سیالات نیازمند انتخابهای طراحی دقیق، مانند استفاده از سیلهای بالانس برای کاهش بارگذاری سطح و انتخاب ترکیبات مواد سطحی (اغلب شامل کربن گرافیت به دلیل خواص خود روانکاری آن) است که بتوانند شرایط روانکاری مرزی یا مختلط را بدون سایش یا تولید حرارت بیش از حد تحمل کنند.
سایندگی / محتوای جامدات
وجود ذرات ساینده (ماسه، کاتالیزورهای ریز، رسوب، کریستالها) در سیال فرآیندی برای مکانیکال سیل ها بسیار مضر است. این ذرات در فیلم سیال بین سطوح گیر کرده و باعث سایش سریع ساینده میشوند که معمولاً به صورت شیارهای متحدالمرکز یا خراشیدگی سنگین روی سطوح دیده میشود. مواد ساینده همچنین میتوانند به آببندهای ثانویه آسیب رسانده و باعث سایش سایر اجزای سیل شوند. استراتژیهای مقابله با مواد ساینده شامل انتخاب ترکیبات مواد سطح بسیار سخت (مانند کاربید سیلیکون در مقابل کاربید سیلیکون، یا کاربید تنگستن در مقابل کاربید تنگستن) که در برابر خراشیدگی مقاوم هستند، استفاده از کنترلهای محیطی مانند جداکنندههای سیکلونی (API Plan 31) برای حذف جامدات از جریان فلاش، تزریق فلاش تمیز خارجی (API Plan 32) برای جداسازی سیل از سیال فرآیندی ساینده، یا به کارگیری سیلهای دوبل که در آن یک سیال مانع تمیز سطوح را روانکاری میکند، میشود.
خورندگی
حمله شیمیایی میتواند تمام اجزای سیلی را که با سیال فرآیندی در تماس هستند، تخریب کند. سطوح سیل میتوانند دچار حفرهدار شدن یا خوردگی عمومی شوند. آببندهای ثانویه الاستومری میتوانند متورم، سخت، ترکخورده یا حل شوند. اجزای فلزی مانند فنرها، بلوزها و سختافزارها میتوانند خورده شده و منجر به از دست دادن عملکرد یا شکستگی شوند. انتخاب دقیق مواد مقاوم شیمیایی برای تمام قطعات مرطوب، بر اساس مواد شیمیایی خاص موجود (از جمله اجزای جزئی و عوامل تمیزکننده) و دمای عملیاتی، ضروری است. باید به جداول سازگاری شیمیایی و دادههای سازنده مراجعه کرد. در کاربردهای بسیار خورنده، ممکن است نیاز به سیلهای نصب خارجی، سیلهای غیر فلزی، سیلهای بلوز فلزی ساخته شده از آلیاژهای مقاوم (مانند Hastelloy® یا Alloy 276) یا سیلهای دوبل با سیال مانع سازگار باشد.
محتوای جامدات / کریستالیزاسیون / پلیمریزاسیون
سیالاتی که حاوی جامدات معلق هستند، یا آنهایی که تمایل به کریستالیزه شدن، جامد شدن، کک شدن یا پلیمریزه شدن به دلیل تغییرات دما، فشار یا قرار گرفتن در معرض هوا دارند، چالشهای قابل توجهی ایجاد میکنند. این مواد میتوانند در اطراف اجزای سیل جمع شده، مکانیزمهای فنر یا بلوز را مسدود کنند، از حرکت محوری عناصر آببندی ثانویه سیلهای پوشر جلوگیری کنند (گیر کردن دینامیکی) و باعث سایش ساینده یا لبپریدگی سطوح سیل شوند. استراتژیها شامل استفاده از طراحیهای سیل کمتر مستعد گرفتگی، تأمین فلاش تمیز (Plan 32)، استفاده از کوئنچ (Plan 62، اغلب بخار یا آب) در سمت اتمسفری برای حل کردن یا شستشوی رسوبات، یا به کارگیری ژاکتهای گرمایشی/سرمایشی برای حفظ سیال در حالت مایع در داخل محفظه سیل است.
فشار بخار / تبخیر ناگهانی (Flashing)
هر مایعی دارای فشار بخاری است که با دما افزایش مییابد. اگر فشار در محفظه سیل به زیر فشار بخار سیال در دمای عملیاتی کاهش یابد، فیلم سیال بین سطوح سیل میتواند بخار شود یا “تبخیر ناگهانی” (Flash) رخ دهد. این پدیده بهویژه هنگام آببندی سیالات نزدیک به نقطه جوش یا هیدروکربنهای سبک مرتبط است. تبخیر ناگهانی باعث از دست دادن روانکاری شده و منجر به کارکرد خشک، اصطکاک بالا، آسیب احتمالی سطح (لبپریدگی، شوک حرارتی، ترکهای حرارتی)، صدا (ترق تروق یا جیغ) و نشتی نامنظم میشود. حفظ حاشیه فشار بخار کافی (اختلاف بین فشار محفظه سیل و فشار بخار سیال) بسیار مهم است. این امر را میتوان با خنک کردن سیال محفظه سیل (API Plan 21, 23) برای کاهش فشار بخار آن یا با افزایش فشار محفظه سیل (به عنوان مثال، با استفاده از API Plan 11 با بوش گلویی مناسب) به دست آورد. سیلهای بالانس نیز عموماً برای سیالات با فشار بخار بالا ترجیح داده میشوند.
نقش دوگانه سیال فرآیندی به عنوان هم محیط آببندی شده و هم روانکننده/خنککننده ضروری، خواص آن را در شرایط عملیاتی واقعی داخل محفظه سیل به یک عامل اصلی در بقای سیل تبدیل میکند.
وضعیت پمپ و دینامیک سیستم
سلامت مکانیکی و دینامیک عملیاتی خود پمپ تأثیر مستقیم و قابل توجهی بر عمر سیل دارد. سیلی که در پمپی با نگهداری ضعیف یا عملکرد نامناسب نصب شده باشد، صرف نظر از کیفیت سیل، محکوم به خرابی زودهنگام است.
همراستایی
همراستایی دقیق نه تنها بین شفتهای پمپ و محرک، بلکه همچنین تضمین عمود بودن سطح محفظه سیل نسبت به محور شفت و هممرکزی سوراخ محفظه سیل با شفت، بسیار مهم است. ناهمراستایی باعث بارگذاری ناهموار بر روی سطوح سیل شده و منجر به لرزش، ارتعاش، سایش تسریع شده و نشتی میشود. همراستایی باید در حین نصب و به صورت دورهای پس از آن بررسی شود، زیرا ممکن است به دلیل عواملی مانند انبساط حرارتی، کشش لولهها و نشست فونداسیون تغییر کند. API 682 محدودیتهای تلرانس خاصی را برای این پارامترها ارائه میدهد.
پایداری شفت (لنگی، انحراف، بازی محوری)
شفت پمپ باید به نرمی و پایداری بچرخد. لنگی بیش از حد شفت (نشاندهنده خم بودن شفت)، انحراف دینامیکی شفت (اغلب ناشی از نیروهای هیدرولیکی هنگام کار دور از BEP یا به دلیل سفتی ناکافی شفت)، یا بازی محوری (معمولاً ناشی از مشکلات یاتاقان) مانع از حفظ تماس ثابت و صاف سطوح سیل میشود. این منجر به لرزش سطح، ارتعاش، سایش ناهموار، آسیب ضربهای احتمالی و نشتی میشود. این پارامترها باید قبل از نصب سیل اندازهگیری و تأیید شوند که در محدوده قابل قبول (اغلب توسط API 610 یا API 682 مشخص میشود) قرار دارند.
سلامت یاتاقانها
وضعیت یاتاقانهای پمپ مستقیماً با قابلیت اطمینان سیل مرتبط است. یاتاقانهای فرسوده یا آسیبدیده منبع اصلی لرزش و ناپایداری شفت (لنگی، بازی محوری) هستند که، همانطور که بحث شد، عمر سیل را به شدت کوتاه میکند. برعکس، نشتی بیش از حد سیل میتواند روانکننده یاتاقان را آلوده کرده و منجر به خرابی زودهنگام یاتاقان شود. حفظ سلامت یاتاقانها از طریق روانکاری مناسب و نظارت بر وضعیت، برای طول عمر سیل ضروری است.
نقطه عملیاتی (BEP)
پمپهای سانتریفیوژ برای کارکرد با بیشترین راندمان و پایداری در نقطه بهترین راندمان (BEP) خود طراحی شدهاند. کارکرد پمپ به طور قابل توجهی دور از BEP (چه در جریان بسیار کم و چه در جریان بسیار زیاد) بارهای هیدرولیکی شعاعی بالایی را بر روی پروانه و شفت القا کرده و باعث انحراف شفت میشود. این انحراف منجر به افزایش لرزش، تماس احتمالی بین قطعات چرخان و ثابت و بارگذاری ناهموار بر روی سطوح سیل میشود که همگی به کاهش عمر سیل کمک میکنند. کارکرد دور از BEP همچنین میتواند خطر کاویتاسیون را افزایش دهد، که پالسهای فشار و لرزش آسیبرسان به سیلها ایجاد میکند. کارکرد پمپ نزدیک به BEP طراحی شده آن، هم برای راندمان پمپ و هم برای قابلیت اطمینان سیل بسیار مهم است.
نقش حیاتی نصب و جابجایی
حتی بهترین سیل، که کاملاً با کاربرد مطابقت داشته و در پمپی سالم نصب شده باشد، اگر به درستی نصب نشود، میتواند به سرعت خراب شود. شیوههای نصب نادرست به طور مداوم به عنوان یکی از علل اصلی خرابی زودهنگام سیل مکانیکی ذکر میشود.
خطاهای رایج عبارتند از:
- آسیب در حین جابجایی: سطوح سیل، بهویژه مواد شکننده مانند سرامیک یا کاربید سیلیکون، در صورت افتادن یا جابجایی نادرست قبل یا در حین نصب، به راحتی میتوانند لبپریده یا خراشیده شوند. الاستومرها میتوانند روی لبههای تیز یا رزوهها بریده یا زخمی شوند.
- آلودگی: عدم تمیز کردن کامل سطوح شفت، غلاف و محفظه سیل قبل از نصب، میتواند باعث شود کثیفی، شن یا زبالههای قدیمی در نشیمنگاه مناسب اختلال ایجاد کرده یا به اجزای سیل آسیب برسانند.
- تنظیم/فشردگی نادرست: سیلهای کامپوننتی نیاز به موقعیتدهی محوری دقیق برای دستیابی به فشردگی صحیح فنر دارند. فشردگی بیش از حد منجر به بارگذاری بیش از حد سطح، گرما و سایش میشود، در حالی که فشردگی کمتر از حد، منجر به بار ناکافی سطح و نشتی میشود. سیلهای کارتریجی این کار را با دستگاههای تنظیم از پیش تعیین شده ساده میکنند.
- ناهمراستایی اجزا: اطمینان از نصب عمود سیت ثابت در گلند و پیچ شدن یکنواخت گلند به محفظه پمپ برای جلوگیری از ناهمراستایی سطح و بارگذاری ناهموار بسیار مهم است.
- روانکاری نامناسب: استفاده از روانکننده ناسازگار یا مقدار ناکافی آن بر روی الاستومرها در حین مونتاژ میتواند باعث پارگی، پیچ خوردگی (خرابی مارپیچی) یا گیر کردن آنها شود. استفاده از گریس روی بلوزها اغلب توصیه نمیشود.
- گشتاور نادرست: سفت کردن بیش از حد پیچهای گلند میتواند گلند و سیت ثابت را تغییر شکل داده و منجر به مشکلات صافی سطح و نشتی شود. سفت کردن بیش از حد پیچهای تنظیم میتواند به شفت/غلاف آسیب برساند.
علاوه بر این، شرایط نگهداری مناسب (محیط تمیز، خشک، با دمای کنترل شده، محافظت شده از آسیب) قبل از نصب ضروری است تا اطمینان حاصل شود که سیل در زمان نیاز در وضعیت بهینه قرار دارد.
ارتباط متقابل این عوامل را نمیتوان نادیده گرفت. مشکلی در یک ناحیه، مانند ناهمراستایی، اغلب باعث ایجاد مشکلاتی در نواحی دیگر میشود، مانند لرزش و سایش ناهموار سطح. رسیدگی صرف به علامت (مانند تعویض سیل فرسوده) بدون شناسایی و اصلاح علت ریشهای (مانند ناهمراستایی) ناگزیر منجر به خرابیهای مکرر خواهد شد. دیدگاهی جامع، با در نظر گرفتن سیل، پمپ، سیال فرآیندی، شرایط عملیاتی و شیوههای نگهداری به عنوان یک سیستم یکپارچه، برای دستیابی به عملکرد آببندی قابل اعتماد و بلندمدت ضروری است.
“`
بخش ۳: نگهداری پیشگیرانه برای افزایش قابلیت اطمینان
فراتر رفتن از رویکرد صرفاً واکنشی – یعنی منتظر ماندن برای خرابی سیل قبل از اقدام – برای به حداکثر رساندن طول عمر سیل و به حداقل رساندن توقف پرهزینه، امری اساسی است. اجرای یک استراتژی نگهداری پیشگیرانه و پیشبینانه شامل بازرسیهای منظم، پایش دقیق شرایط عملیاتی، مدیریت دقیق محیط سیل و رسیدگی به مشکلات بالقوه قبل از تبدیل شدن به خرابی است.
توسعه یک برنامه نگهداری مؤثر (بررسیها و بازرسیهای روتین)
یک برنامه بازرسی ساختاریافته امکان تشخیص زودهنگام تغییرات جزئی را که ممکن است نشاندهنده مشکلات در حال توسعه باشند، فراهم میکند. در حالی که فواصل زمانی خاص به اهمیت تجهیزات، شرایط عملیاتی و خواص سیال بستگی دارد، دستورالعملهای کلی برگرفته از شیوههای نگهداری پمپ میتواند نقطه شروعی را ارائه دهد.
- بررسیهای روزانه/شیفتی: این بررسیها بر پارامترهای قابل مشاهده آسان تمرکز دارند.
- نشتی قابل مشاهده: ناحیه گلند سیل، پایه پمپ و کف اطراف را برای هرگونه چکه یا تجمع سیال فرآیندی یا سیال مانع/بافر بررسی کنید. هرگونه تغییر نسبت به مشاهدات قبلی را یادداشت کنید.
- صدای شنیداری: به صداهای غیرعادی که از ناحیه پمپ یا سیل میآید، مانند صدای سایش، مالش، ترق تروق، جیغ یا صدای بیش از حد کاویتاسیون گوش دهید.
- دمای یاتاقان: محفظه یاتاقانها را لمس کنید (با احتیاط) یا از دماسنج تماسی/تفنگ مادون قرمز برای بررسی گرمای بیش از حد استفاده کنید.
- لرزش: اگر مجهز به پایش دائمی است، سطوح لرزش را بررسی کنید. در غیر این صورت، پرسنل باتجربه ممکن است بتوانند تغییرات قابل توجه را با لمس تشخیص دهند (با احتیاط).
- سطح و وضعیت روانکننده/سیستم پشتیبانی: سطح روغن در محفظه یاتاقانها (شیشههای رویت) را بررسی کنید. سطح، فشار و دمای گیجهای سیستمهای پشتیبانی سیل (مخازن، آکومولاتورها) را بررسی کنید. شفافیت و رنگ روانکنندهها/سیالات مانع را بررسی کنید؛ به دنبال نشانههای آلودگی آب یا کف کردن باشید.
- بررسیهای ماهانه/فصلی: این شامل بازرسیهای دقیقتر و وظایف نگهداری جزئی است.
- روانکاری: در صورت نیاز سطح روغن یاتاقانها را تنظیم کنید. یاتاقانهای موتور و پمپ را طبق توصیههای سازنده (اغلب بر اساس ساعات کار یا فاصله زمانی، مثلاً هر 2000 ساعت یا 3 ماه) گریسکاری کنید. روغن یاتاقان را طبق برنامه (فاصله زمانی مشابه گریسکاری) تعویض کنید. حبابهای روغندان/شیشههای رویت را تمیز کنید.
- تمیزکاری: زبالههای خارجی را از پمپ، براکتهای یاتاقان و موتور تمیز کنید.
- بررسیهای مکانیکی: سفتی پیچهای پایه پمپ را بررسی کنید. وضعیت کوپلینگ شفت را بازرسی کنید. همراستایی شفت پمپ-موتور را تأیید کنید. فشارهای مکش و تخلیه را بررسی کنید.
- سیستم پشتیبانی سیل: اجزای سیستم فلاش (فیلترها، صافیها، شیرها، لولهکشی، خنککنندهها) را از نظر تمیزی، نشتی یا انسداد بازرسی کنید. در صورت امکان، فشار پیششارژ آکومولاتور (Plan 53B/C) را بررسی کنید.
- بررسیهای سالانه (معمولاً در طول توقفهای برنامهریزی شده/تعمیرات اساسی): این امکان بازرسیهای تهاجمیتری را که نیاز به دمونتاژ تجهیزات دارند، فراهم میکند.
- بازرسی سیل: سیل مکانیکی را جدا کرده و اجزای آن را با دقت بازرسی کنید. سطوح سیل را از نظر الگوهای سایش، لبپریدگی، ترکخوردگی، ترکهای حرارتی، شیاردار شدن یا رسوبات بررسی کنید. آببندهای ثانویه (الاستومرها، بلوزها) را از نظر آسیب، تورم، سخت شدن یا تغییر شکل دائمی (Compression Set) بازرسی کنید. فنرها را از نظر خوردگی یا شکستگی بررسی کنید. غلاف را از نظر سایش، فرتینگ یا آسیب زیر آببندهای ثانویه یا پیچهای تنظیم بازرسی کنید.
- اجزای داخلی پمپ: پروانه را از نظر فرسایش، خوردگی یا پرههای خم شده بازرسی کنید. محفظه (Casing) را از نظر سایش، خوردگی یا حفرهدار شدن بازرسی کنید. محفظه سیل/درپوش جعبه آببندی را از نظر حفرهدار شدن، ترک، فرسایش یا سایش بررسی کنید.
- بررسیهای مکانیکی: لنگی شفت و بازی محوری را اندازهگیری کنید. وضعیت محفظه یاتاقان را بررسی کنید.
- نقطه تصمیمگیری: بر اساس ارزیابی وضعیت، تصمیم بگیرید که آیا سیل موجود را تعمیر کنید (اگر امکانپذیر و اقتصادی باشد) یا آن را با یک سیل جدید جایگزین کنید. هرگونه قطعه فرسوده پمپ را تعویض کنید.
نگهداری مؤثر نیازمند مستندسازی دقیق است. نگهداری گزارشهای دقیق از تمام بازرسیها، یافتهها، اقدامات نگهداری انجام شده (شامل تاریخ، قطعات استفاده شده، پرسنل)، شرایط عملیاتی (فشارها، دماها، جریانها)، پارامترهای سیستم پشتیبانی سیل و هرگونه خرابی رخ داده، بسیار مهم است. این تاریخچه دادههای ارزشمندی را برای عیبیابی مشکلات آینده، شناسایی مشکلات تکراری، تشخیص روندها و بهینهسازی استراتژیهای نگهداری فراهم میکند. صرفاً انجام وظایف برنامهریزی شده بدون ارزیابی اثربخشی آنها یا درک وضعیت اساسی، ارزش محدودی دارد.
جدول ۱: نمونه چک لیست نگهداری سیل مکانیکی
تناوب | بررسی/اقدام خاص | معیار پذیرش / نکات کلیدی | ثبت یافتهها؟ |
---|---|---|---|
روزانه/شیفتی | بررسی بصری نشتی سیل | انتظار نشتی قابل مشاهده صفر (به جز چکههای جزئی اولیه). هرگونه چکه/تجمع را گزارش دهید. | بله (در صورت غیرعادی بودن) |
روزانه/شیفتی | گوش دادن به صدای غیرعادی سیل/پمپ | بدون صدای جیغ، ترق تروق، سایش. تغییرات را گزارش دهید. | بله (در صورت غیرعادی بودن) |
روزانه/شیفتی | بررسی سطح/فشار/دمای سیستم پشتیبانی سیل (در صورت وجود) | در محدوده عملیاتی مشخص. نشتیها را بررسی کنید. | بله |
هفتگی | بررسی دمای یاتاقان پمپ (تفنگ مادون قرمز/لمس) | معمولاً کمتر از 70-80 درجه سانتیگراد (160-180 درجه فارنهایت)، پایه مشخص شده. افزایش قابل توجه را گزارش دهید. | بله |
هفتگی | بررسی سطح روانکننده محفظه یاتاقان (شیشه رویت) | سطح صحیح، روغن شفاف. سطح پایین یا آلودگی را گزارش دهید. | بله |
هفتگی | بررسی خطوط فلاش سیل (بصری) | بدون نشتی، انسداد یا لرزش بیش از حد. | بله (در صورت غیرعادی بودن) |
ماهانه | بررسی لرزش پمپ/موتور (آنالایزر قابل حمل/لمس) | مقایسه با پایه/حدود. افزایشها را گزارش دهید. | بله |
ماهانه | بازرسی اجزای سیستم پشتیبانی سیل (خنککننده، فیلتر و غیره) | تمیز، بدون نشتی، جریان صحیح در صورت وجود نشانگر. | بله (در صورت غیرعادی بودن) |
فصلی | بررسی همراستایی پمپ/موتور (در صورت نیاز بر اساس لرزش/تاریخچه) | در محدوده تلرانس (مثلاً کمتر از 0.002 اینچ آفست). | بله |
فصلی | روانکاری یاتاقانها (گریس یا تعویض روغن) | طبق برنامه سازنده. از نوع/مقدار صحیح روانکننده استفاده کنید. | بله |
سالانه (حین توقف) | اندازهگیری لنگی شفت و بازی محوری | در محدوده پمپ/API (مثلاً کمتر از 0.002 اینچ TIR لنگی، کمتر از 0.005 اینچ بازی محوری). | بله |
سالانه (حین توقف) | بررسی عمود بودن سطح محفظه/گلند سیل | در محدوده تلرانس (مثلاً کمتر از 0.0005 اینچ بر اینچ قطر TIR). | بله |
سالانه (حین توقف) | بررسی هممرکزی سوراخ محفظه سیل | در محدوده تلرانس (مثلاً کمتر از 0.005 اینچ TIR). | بله |
سالانه (حین توقف) | جداسازی و بازرسی سیل (سطوح، الاستومرها، سختافزار) | ارزیابی سایش، آسیب، رسوبات. تصمیم: تعمیر یا تعویض. | بله (با جزئیات) |
سالانه (حین توقف) | بازرسی اجزای داخلی سیستم پشتیبانی سیل | تمیز کردن مخزن، بررسی ابزار دقیق، تمیز کردن/تعویض فیلترها. | بله |
در صورت نیاز | رسیدگی سریع به هرگونه نشتی، صدا، دمای بالا، لرزش بالا | علائم هشدار دهنده را نادیده نگیرید. علت ریشهای را بررسی کنید. | بله |
توجه: بررسیها، فواصل زمانی و معیارهای خاص باید بر اساس توصیههای سازنده تجهیزات، شرایط فرآیندی، خواص سیال، استانداردهای API (در صورت کاربرد) و تجربیات سایت تطبیق داده شوند.
پایش و فناوریهای پیشبینانه
فراتر از بازرسیهای برنامهریزی شده، تکنیکهای نگهداری پیشبینانه (PdM) از فناوریهای پایش برای ارزیابی وضعیت واقعی تجهیزات و پیشبینی خرابیهای بالقوه قبل از وقوع استفاده میکنند. این امکان میدهد که نگهداری فقط در صورت لزوم انجام شود، تخصیص منابع بهینه شده و مداخلات غیر ضروری به حداقل برسد.
- آنالیز ارتعاشات: این احتمالاً قدرتمندترین ابزار برای ارزیابی سلامت مکانیکی تجهیزات دوار، از جمله پمپ، یاتاقانها، کوپلینگ و موتور است که همگی بر عمر سیل تأثیر میگذارند. پایش منظم ارتعاشات با استفاده از آنالایزرهای قابل حمل یا سنسورهای نصب شده دائمی میتواند موارد زیر را تشخیص دهد:
- عدم تعادل
- ناهمراستایی (زاویهای، موازی، داخلی)
- نقص یاتاقانها (مشکلات رینگ داخلی، رینگ خارجی، ساچمه/غلتک، قفسه)
- شل بودن مکانیکی (پیچهای پایه، لقی یاتاقان)
- مالش شفت
- مشکلات هیدرولیکی مانند کاویتاسیون یا توربولانس
- مشکلات درگیری دنده (در صورت وجود)
- مشکلات الکتریکی در موتور
با شناسایی زودهنگام این مشکلات، میتوان قبل از اینکه باعث خرابی فاجعهبار یاتاقان یا انحراف شدید شفت شوند که سیل را از بین میبرد، اقدام اصلاحی انجام داد. تحلیل روند دادههای ارتعاشی در طول زمان بسیار ارزشمند است.
- پایش دما: ردیابی دمای یاتاقانهای پمپ، ناحیه گلند سیل و سیالات سیستم پشتیبانی سیل، بینشهای حیاتی را فراهم میکند. ترموگرافی مادون قرمز امکان نقشهبرداری دمایی بدون تماس تجهیزات را فراهم میکند. افزایش ناگهانی یا روندی دما میتواند نشاندهنده موارد زیر باشد:
- از دست دادن روانکاری (یاتاقانها یا سطوح سیل)
- اصطکاک بیش از حد (تماس سطوح سیل، یاتاقان در حال خرابی)
- عملکرد نادرست سیستم خنککاری (گرفتگی خنککننده، قطع آب خنککننده)
- آسیب سطح سیل منجر به افزایش تولید گرما
- جریان ناکافی فلاش
ایجاد دماهای پایه و پایش انحرافات، کلیدی است.
- پایش سیستم پشتیبانی سیل (فشار، سطح، جریان): برای پمپهای مجهز به سیلهای دوبل یا سیلهای تکی با پلانهای فلاش کمکی، سیستم پشتیبانی سیل اطلاعات تشخیصی حیاتی را فراهم میکند.
- فشار: پایش فشار سیال مانع (Plan 53A/B/C, 54) یا فشار سیال بافر (Plan 52) ضروری است. افت فشار مانع نشاندهنده نشتی از سیل داخلی یا خارجی (یا نشتی سیستم) است. افزایش فشار بافر (Plan 52) نشاندهنده نشتی سیال فرآیندی از سیل داخلی است. حفظ اختلاف فشار صحیح برای عملکرد مناسب حیاتی است.
- سطح: پایش سطح سیال در مخزن (Plan 52, 53A/B/C) نشاندهنده مصرف یا نشتی سیال است. کاهش سطح در سیستم مانع (Plan 53) به نشتی سیل (داخلی یا خارجی) اشاره دارد. افزایش سطح در سیستم بافر (Plan 52) نشاندهنده نشتی سیال فرآیندی به سیستم بافر است. میتوان فرکانس پر کردن مجدد را برای ارزیابی وضعیت سیل ردیابی کرد.
- جریان: اندازهگیری نرخ جریان سیال فلاش (Plan 11, 32) یا گردش سیال مانع/بافر (Plan 21, 23, 41, 53B/C, 54) تأیید میکند که سیستم پشتیبانی به درستی کار میکند. جریان کاهش یافته میتواند نشاندهنده انسداد، سایش پمپ (در سیستمهای Plan 54) یا مشکلات شیر کنترل باشد. ابزار دقیق روی این سیستمها باید به طور منظم کالیبره شده و مورد اعتماد باشد. به طور فزایندهای، این پارامترها از طریق سیستمهای کنترل کارخانه از راه دور پایش میشوند که امکان ردیابی و هشداردهی در زمان واقعی را فراهم میکند.
- آنالیز روغن: نمونهبرداری منظم و آنالیز روغن روانکننده یاتاقان میتواند هشدار زودهنگامی از سایش یاتاقان (از طریق آنالیز ذرات سایش)، تخریب روانکننده (تغییرات ویسکوزیته، اکسیداسیون) و آلودگی (آب، سیال فرآیندی) ارائه دهد. این به طور غیرمستقیم با تضمین سلامت یاتاقان از قابلیت اطمینان سیل پشتیبانی میکند. آنالیز سیال مانع/بافر سیل نیز میتواند آلودگی یا تخریب را تشخیص دهد.
- تشخیص نشت: در حالی که بررسیهای بصری اساسی هستند، روشهای پیچیدهتری میتوانند برای خدمات حیاتی یا تشخیص نشتیهای بسیار کوچک به کار گرفته شوند. اینها ممکن است شامل سنسورهای نشر آکوستیک یا آشکارسازهای گاز (“نشتیابها”) باشند که در نزدیکی گلند سیل قرار میگیرند، بهویژه برای نشتی بخارات خطرناک.
ادغام دادهها از چندین فناوری PdM تصویر کاملتری از سلامت تجهیزات ارائه میدهد و دقت تشخیصی را بهبود میبخشد. به عنوان مثال، افزایش لرزش همراه با افزایش دمای یاتاقان قویاً نشاندهنده مشکل یاتاقان است، در حالی که افت فشار سیال مانع بدون تغییر در لرزش ممکن است به نشتی سیل خارجی اشاره کند.
کنترلهای محیطی سیل (API Flush Plans)
اغلب، سیال فرآیندی یا شرایط عملیاتی درون محفظه سیل پمپ ذاتاً برای عملکرد قابل اطمینان و بلندمدت سیل نامناسب هستند. سیستمهای کنترل محیطی سیل، که اغلب به عنوان پلانهای فلاش API (همانطور که در API 682 استاندارد شده است) نامیده میشوند، شرایط را مستقیماً در اطراف سطوح سیل تغییر میدهند تا محیط مطلوبتری ایجاد کنند. انتخاب، بهرهبرداری و نگهداری مناسب این پلانها برای بقای سیل در کاربردهای چالشبرانگیز حیاتی است.
اهداف رایج کنترلهای محیطی عبارتند از:
- خنککاری: حذف حرارت تولید شده در سطوح سیل یا هدایت شده از سیال فرآیندی (API Plans 11, 13, 21, 23, 31, 32, 41, 53A/B/C, 54).
- بهبود روانکاری: تأمین سیال تمیزتر یا با روانکنندگی بهتر به سطوح سیل (API Plans 11, 13, 31, 32, 53A/B/C, 54).
- مدیریت فشار: افزایش فشار در محفظه سیل برای بهبود حاشیه فشار بخار (API Plan 11, 13 با بوش گلویی) یا کاهش آن (API Plan 12).
- حذف جامدات: جلوگیری از رسیدن ذرات ساینده به سطوح سیل (API Plans 11, 13, 31, 32, 53A/B/C, 54).
- جلوگیری از رسوبات: شستشوی موادی که میتوانند جامد، کریستالیزه یا کک شوند (API Plans 11, 32, 62).
- مهار: تأمین مهار ثانویه برای سیالات خطرناک (API Plan 52, 72, 75, 76).
- حذف هوا: جلوگیری از ورود هوا به فرآیند یا واکنش با سیال فرآیندی در سطوح سیل (API Plan 62, 53A/B/C, 54).
جنبههای کلیدی نگهداری برای پلانهای فلاش:
- اطمینان از جریان و فشار مناسب: به طور منظم تأیید کنید که نرخ جریان و فشارهای مشخص شده برای سیالات فلاش، مانع یا بافر حفظ میشوند. گیجها، فلومترها و شیرهای کنترل را بررسی کنید.
- حفظ کیفیت سیال: اطمینان حاصل کنید که سیال فلاش/مانع/بافر تمیز است و مشخصات مورد نیاز را برآورده میکند. آلودگی یا تخریب را بررسی کنید. سیالات را طبق برنامه تعویض کنید.
- تمیز نگه داشتن خطوط و اجزا: لولهکشی، اوریفیسها، فیلترها، صافیها، جداکنندههای سیکلونی و مبدلهای حرارتی را از نظر گرفتگی یا رسوب بازرسی کنید. اجزا را در صورت نیاز تمیز یا تعویض کنید. گرفتگی اوریفیسها در خطوط بازچرخشی (Plan 11, 13, 21, 23) علت رایج گرم شدن بیش از حد سیل است. خنککنندههای مسدود شده (Plan 21, 23, 41, 53A/B/C, 54) منجر به دماهای بالا میشوند.
- بررسی عملکرد مبدل حرارتی: از جریان کافی محیط خنککننده (آب، هوا) به مبدلهای حرارتی اطمینان حاصل کنید و تأیید کنید که خنککاری کافی را ارائه میدهند (پایش دمای ورودی/خروجی). لولهها/پرهها را در صورت نیاز تمیز کنید.
- تأیید ابزار دقیق: گیجهای فشار، ترانسمیترهای سطح، فلومترها و سنسورهای دما را به صورت دورهای کالیبره کنید تا از صحت خوانشها اطمینان حاصل شود.
- سیستمهای Plan 53: سطوح صحیح مخزن و فشارهای پیششارژ گاز (Plan 53B/C) را حفظ کنید. اطمینان حاصل کنید که رینگ پمپاژ (Plan 53B/C) یا پمپ خارجی (Plan 54) سیال مانع را به طور مؤثر به گردش در میآورد.
- سیستمهای Plan 52: سطح و فشار مخزن را برای نشانههای نشتی سیل داخلی پایش کنید. اطمینان حاصل کنید که ونت تمیز و فعال است.
عدم نگهداری صحیح سیستم پشتیبانی سیل، هدف آن را نفی کرده و میتواند منجر به خرابی سریع سیل شود، که اغلب حالتهای خرابی مشابه شرایطی را تقلید میکند که سیستم پشتیبانی برای کاهش آنها طراحی شده بود (مانند گرم شدن بیش از حد به دلیل خنککننده مسدود، سایش ساینده به دلیل جداکننده سیکلونی مسدود). سیستم پشتیبانی باید به عنوان بخشی جداییناپذیر و حیاتی از سیستم آببندی در نظر گرفته شود.
با ترکیب بازرسیهای برنامهریزی شده، پایش پیشبینانه و نگهداری دقیق کنترلهای محیطی، تأسیسات میتوانند از واکنش به خرابیهای سیل به مدیریت پیشگیرانه سلامت سیل تغییر جهت دهند و به طور قابل توجهی MTBF را افزایش داده و قابلیت اطمینان کلی کارخانه را بهبود بخشند.
بخش ۴: بهترین شیوهها برای نصب سیل مکانیکی
همانطور که قبلاً مشخص شد، نصب نادرست یکی از عوامل اصلی خرابی زودهنگام سیل مکانیکی است. پایبندی به بهترین شیوهها در طول فرآیند نصب برای دستیابی به عمر مورد انتظار سیل، غیرقابل اجتناب است. استفاده از سیلهای کارتریجی به طور قابل توجهی این فرآیند را ساده کرده و پتانسیل خطا را کاهش میدهد، که آنها را به گزینه ترجیحی در صورت امکان تبدیل میکند.
بررسیهای پیش از نصب: زمینهسازی برای موفقیت
قبل از اقدام به نصب هر سیلی، باید یک سری بررسیهای حیاتی روی خود پمپ انجام شود. این بررسیها تضمین میکنند که تجهیزات یک پلتفرم پایدار و با ابعاد صحیح برای کارکرد سیل فراهم میکنند. نادیده گرفتن این مراحل اساساً فرآیند نصب را تضعیف میکند.
- لنگی شفت (TIR – Total Indicator Reading): یک ساعت اندیکاتور را روی یک نقطه ثابت و محکم (مانند محفظه یاتاقان) با نوک اندیکاتور عمود بر سطح شفت در ناحیهای که سیل قرار میگیرد، نصب کنید. شفت را به آرامی با دست بچرخانید (360 درجه) و حداکثر انحراف اندیکاتور را ثبت کنید. لنگی بیش از حد (معمولاً > 0.002 اینچ یا 0.05 میلیمتر TIR، اگرچه مشخصات سازنده پمپ/سیل یا API 682 را بررسی کنید) نشاندهنده خم بودن شفت است که باعث لرزش سطح سیل و خرابی زودهنگام میشود. اگر لنگی از حد مجاز بیشتر است، نصب را ادامه ندهید. ابتدا مشکل خم بودن شفت را برطرف کنید.
- بازی محوری شفت (End Play): ساعت اندیکاتور را طوری نصب کنید که نوک آن موازی با شفت باشد و با انتهای شفت یا یک لبه شفت تماس داشته باشد. شفت را کاملاً در یک جهت محوری فشار دهید، اندیکاتور را صفر کنید، سپس شفت را کاملاً در جهت مخالف بکشید. کل حرکت را ثبت کنید. بازی محوری بیش از حد (معمولاً > 0.005 اینچ یا 0.13 میلیمتر، مشخصات را بررسی کنید) معمولاً نشاندهنده یاتاقانهای فرسوده یا تنظیم نادرست است. این امر اجازه حرکت محوری بیش از حدی را میدهد که سیل ممکن است نتواند آن را تطبیق دهد و منجر به نشتی یا آسیب میشود. قبل از نصب سیل، یاتاقانها را تعمیر کنید.
- لنگی سطح محفظه سیل (عمود بودن نسبت به شفت): ساعت اندیکاتور را روی شفت (ایدهآل با یک براکت چرخان، یا با دقت شفت را با اندیکاتور ثابت شده به محفظه یاتاقان بچرخانید) با نوک اندیکاتور در تماس با سطح ماشینکاری شده محفظه سیل (جایی که گلند سیل پیچ میشود) نصب کنید. شفت را 360 درجه بچرخانید و TIR را ثبت کنید. لنگی بیش از حد (معمولاً > 0.0005 اینچ بر اینچ قطر سطح محفظه سیل، یا حداکثر 0.005 اینچ TIR، مشخصات را بررسی کنید) به این معنی است که رینگ ثابت سیل عمود بر محور شفت نخواهد بود و باعث بارگذاری ناهموار سطح و سایش سریع میشود. در صورت لزوم، سطح محفظه سیل را دوباره ماشینکاری کنید.
- هممرکزی سوراخ محفظه سیل: ساعت اندیکاتور را روی شفت (یا شفت را بچرخانید) با نوک اندیکاتور در تماس با سوراخ محفظه سیل، جایی که رینگ ثابت سیل یا پایلوت گلند قرار میگیرد، نصب کنید. 360 درجه بچرخانید و TIR را ثبت کنید. خارج از مرکز بودن بیش از حد (معمولاً > 0.005 اینچ یا 0.13 میلیمتر TIR، مشخصات را بررسی کنید) به این معنی است که رینگ ثابت نسبت به رینگ چرخان خارج از مرکز خواهد بود و به طور بالقوه منجر به تماس ناهموار یا گیر کردن پین محرک میشود. در صورت لزوم، سوراخ محفظه سیل را دوباره ماشینکاری کنید.
- وضعیت سطح شفت/غلاف: سطح شفت یا غلاف را در ناحیهای که اجزای سیل (بهویژه آببندهای ثانویه و پیچهای تنظیم) با آن تماس خواهند داشت، به صورت بصری بازرسی کنید. به دنبال پلیسه، لبههای تیز، خراش، شیار، سایش فرتینگ از سیل قبلی یا آسیب ناشی از پیچهای تنظیم باشید. هرگونه نقص میتواند در حین نصب به الاستومرها آسیب برساند یا از آببندی مناسب جلوگیری کند. هرگونه پلیسه یا لبه تیز (مانند جای خار، پلهها) را با سمباده نرم یا سنگ صاف کنید. اگر سطح به طور قابل توجهی آسیب دیده است، ممکن است شفت/غلاف نیاز به تعمیر یا تعویض داشته باشد. اطمینان حاصل کنید که پرداخت سطح با الزامات سازنده سیل مطابقت دارد (اغلب 16-32 µin Ra برای سطوح آببندی اورینگ دینامیکی).
- تمیزی: شفت/غلاف، سوراخ و سطح محفظه سیل و ناحیه پایلوت گلند سیل را کاملاً تمیز کنید. تمام مواد گسکت قدیمی، سیلانت، کثیفی، زنگزدگی، رسوب و باقیماندههای فرآیندی را پاک کنید. از حلالهای مناسب و پارچههای تمیز و بدون پرز استفاده کنید. حتی ذرات کوچک کثیفی میتوانند باعث ناهمراستایی یا آسیب به اجزای شکننده سیل شوند.
انجام دقیق این بررسیها، نصب سیل را از یک اقدام شانسی به یک فرآیند کنترل شده بر پایه یک بنیاد محکم تبدیل میکند.
راهنمای گامبهگام نصب (تمرکز بر سیل کارتریجی)
سیلهای کارتریجی برای نصب مستقیم طراحی شدهاند. در حالی که مراحل خاص ممکن است بین سازندگان و مدلها کمی متفاوت باشد، روش کلی به شرح زیر است:
- تأیید شناسایی سیل: تأیید کنید که شماره قطعه سیل با الزامات پمپ و کاربرد مطابقت دارد. نقشه سیل را برای ابعاد حیاتی (مانند فاصله مورد نیاز از سطح محفظه سیل تا انتهای/لبه شفت، قطر دایره پیچ) بررسی کنید.
- بازرسی سیل جدید: سیل را با دقت از بستهبندی خارج کنید. تمام اجزا را از نظر هرگونه علائم آسیب حمل و نقل به صورت بصری بازرسی کنید، توجه ویژهای به سطوح سیل (بدون لبپریدگی، خراش) و الاستومرها (بدون بریدگی، زدگی) داشته باشید. اطمینان حاصل کنید که گیرهها/صفحات تنظیم محکم در جای خود قرار دارند – اینها سیل را در موقعیت محوری از پیش تعیین شده صحیح نگه میدارند. هنوز گیرههای تنظیم را خارج نکنید.
- آمادهسازی شفت/غلاف: اطمینان حاصل کنید که سطح شفت/غلاف تمیز، صاف و عاری از پلیسه مطابق بررسیهای پیش از نصب است. انتهای شفت یا هر پلهای را کمی پخ بزنید تا از آسیب دیدن الاستومرها در حین نصب جلوگیری شود.
- روانکاری: یک لایه نازک و سازگار از روانکننده را به قطر خارجی شفت/غلاف و قطر داخلی اورینگها یا الاستومر دینامیکی غلاف سیل بمالید. فقط از روانکنندههای توصیه شده توسط سازنده سیل استفاده کنید – اغلب روغن سیلیکون یا روانکننده مخصوص سیل. هرگز از گریس استفاده نکنید مگر اینکه به صراحت مشخص شده باشد، زیرا میتواند مکانیزمهای فنر را مسدود کرده یا در حرکت الاستومر اختلال ایجاد کند. اورینگ/گسکت ثابت روی قطر خارجی گلند پلیت را در جایی که در سوراخ محفظه سیل قرار میگیرد، روانکاری کنید.
- نصب سیل: مجموعه سیل کارتریجی را با دقت روی شفت بلغزانید تا گلند پلیت با سطح محفظه سیل پمپ تماس پیدا کند. از فشار ثابت و یکنواخت استفاده کنید. اگر سیل گیر کرد، آن را بردارید، دوباره از نظر پلیسه یا آلودگی بررسی کنید، دوباره روانکاری کنید و دوباره امتحان کنید. سیل را با زور وارد نکنید. چرخاندن کمی سیل هنگام لغزاندن میتواند به جا افتادن الاستومرها کمک کند. اطمینان حاصل کنید که هرگونه اتصال فلاش/کوئنچ/تخلیه روی گلند پلیت قبل از ادامه به درستی جهتدهی شده است.
- محکم کردن گلند پلیت: مهرهها یا پیچهای گلند را نصب کنید. آنها را به طور یکنواخت و به صورت ضربدری (مانند سفت کردن مهرههای چرخ) سفت کنید تا اطمینان حاصل شود که گلند پلیت به طور مستقیم روی سطح محفظه سیل قرار میگیرد. از چند مرحله سفت کردن استفاده کنید (مثلاً با انگشت سفت، سپس 50% گشتاور، سپس 100% گشتاور). از آچار گشتاورسنج برای اعمال گشتاور صحیح مشخص شده توسط سازنده پمپ یا سیل استفاده کنید. سفت کردن ناهموار میتواند گلند را تغییر شکل داده و سیت ثابت سیل را ناهمراستا کند.
- محکم کردن واحد چرخان: پس از اینکه گلند به طور ایمن پیچ شد، پیچهای تنظیم در کالر سیل را سفت کنید تا بخش چرخان سیل (از طریق غلاف) به شفت پمپ قفل شود. پیچهای تنظیم را به تدریج و به طور متناوب تا گشتاور مشخص شده توسط سازنده سیل سفت کنید. از آچار گشتاورسنج استفاده کنید. اطمینان حاصل کنید که پیچهای تنظیم شفت را به طور ایمن درگیر میکنند بدون اینکه به طور بیش از حد به آن آسیب برسانند.
- برداشتن گیرهها/صفحات تنظیم: این یک مرحله حیاتی است. گیرهها یا صفحات تنظیم را با دقت بردارید و نگه دارید. این دستگاهها اجزای سیل را در موقعیت محوری نسبی صحیح خود در طول نصب نگه میداشتند. برداشتن آنها به فنرها اجازه میدهد تا سطوح سیل را به درستی بارگذاری کنند و سیل را قادر میسازد تا حرکت محوری را تطبیق دهد. عدم برداشتن گیرهها باعث خرابی سریع سیل میشود.
- اتصال لولهکشی کمکی: تمام خطوط مورد نیاز فلاش، کوئنچ، تخلیه، ونت یا سیال مانع/بافر را به پورتهای روی گلند پلیت متصل کنید. اطمینان حاصل کنید که اتصالات بدون نشتی و به درستی مطابق با پلان API مشخص شده مسیریابی شدهاند.
- بررسیهای نهایی: شفت را با دست چندین دور بچرخانید تا اطمینان حاصل شود که آزادانه و بدون صدای گیر کردن یا مالش میچرخد. در صورت به هم خوردن در حین نصب، همراستایی پمپ/محرک را دوباره بررسی کنید.
(برای سیلهای کامپوننتی، فرآیند پیچیدهتر است و شامل اندازهگیری دقیق برای تنظیم موقعیت/فشردگی محوری صحیح، جابجایی دقیق سطوح و الاستومرهای جداگانه و اطمینان از توالی صحیح مونتاژ است. مراجعه به دستورالعملهای دقیق سازنده کاملاً ضروری است.)
جابجایی و اجتناب از اشتباهات رایج
موفقیت به توجه دقیق به جزئیات و اجتناب از اشتباهات رایج بستگی دارد:
- تمیزی بسیار مهم است: با منطقه نصب سیل مانند یک اتاق تمیز رفتار کنید. از آلوده شدن اجزای سیل، بهویژه سطوح، توسط کثیفی، شن، برادههای فلزی یا الیاف پارچه جلوگیری کنید. سیل را تا لحظه نصب در بستهبندی محافظ خود نگه دارید.
- با سطوح با احتیاط رفتار کنید: سطوح سیل با صافی بسیار بالا لپینگ شدهاند و اغلب از مواد شکننده ساخته شدهاند. هرگز سطوح لپینگ شده را با دستهای برهنه (چربی میتواند در مرطوب شدن اختلال ایجاد کند)، ابزار یا پارچههای کثیف لمس نکنید. از انداختن یا ضربه زدن به مجموعه سیل خودداری کنید. حتی آسیب میکروسکوپی میتواند باعث نشتی شود.
- از روانکننده صحیح استفاده کنید: فقط از روانکنندههای تأیید شده توسط سازنده سیل و سازگار با هر دو الاستومر سیل و سیال فرآیندی استفاده کنید. روانکننده را به مقدار کم بمالید – مقدار زیاد میتواند کثیفی را جذب کرده یا در عملکرد اختلال ایجاد کند.
- از اعمال زور خودداری کنید: هرگز سیلی را با چکش یا زور در جای خود قرار ندهید. اگر به راحتی روی آن نمیلغزد، علت را بررسی کنید (پلیسه، ناهمراستایی، اندازه نادرست، عدم روانکاری).
- از عمود بودن اطمینان حاصل کنید: سفت کردن یکنواخت پیچهای گلند برای جلوگیری از کج شدن سیت ثابت بسیار مهم است. از آچار گشتاورسنج استفاده کنید و از الگوی ستارهای پیروی کنید.
- گیرههای تنظیم را فراموش نکنید: عدم برداشتن گیرههای تنظیم سیل کارتریجی پس از نصب، یک خطای شگفتآور رایج و کشنده است.
- جهت چرخش را تأیید کنید: اگر سیل جهتدار است (برخی طراحیها برای عملکرد رینگ پمپاژ یا پیچش فنر به جهت چرخش شفت بستگی دارند)، اطمینان حاصل کنید که برای جهت صحیح چرخش پمپ نصب شده است.
- راهاندازی اولیه: رویههای صحیح راهاندازی پمپ را دنبال کنید. اطمینان حاصل کنید که محفظه سیل ونت شده و قبل از راهاندازی پمپ با مایع پر شده است تا از کارکرد خشک جلوگیری شود. اگر از سیستم پشتیبانی سیل استفاده میکنید، اطمینان حاصل کنید که قبل از راهاندازی پمپ اصلی، راهاندازی شده و به درستی کار میکند (فشار، سطح، جریان صحیح). به سیل اجازه دهید یک دوره کوتاه “آببندی اولیه” داشته باشد؛ ممکن است چکههای جزئی اولیه رخ دهد اما باید به سرعت متوقف شود. در طول کارکرد اولیه، به دقت نشتی، صدا یا گرمای بیش از حد را پایش کنید.
با در نظر گرفتن نصب سیل به عنوان یک کار دقیق که نیازمند آمادهسازی دقیق، اجرای meticulous و پایبندی به دستورالعملهای سازنده است، احتمال دستیابی به عملکرد قابل اعتماد و بلندمدت سیل به طور چشمگیری افزایش مییابد.
بخش پنجم: عیبیابی و خرابیهای رایج سیل مکانیکی
علیرغم بهترین تلاشها در انتخاب، نصب و نگهداری، سیلهای مکانیکی ممکن است همچنان خراب شوند. هنگامی که خرابی رخ میدهد، صرفاً جایگزینی سیل بدون درک علت خرابی، ناکارآمد بوده و احتمالاً منجر به خرابیهای مکرر میشود. یک رویکرد عیبیابی سیستماتیک، شامل بررسی دقیق اجزای سیل خراب شده و ارتباط آن با دادههای عملیاتی، برای شناسایی علت ریشهای و اجرای اقدامات اصلاحی ضروری است.
شناسایی حالتهای خرابی از طریق بازرسی بصری
ظاهر اجزای سیل خراب شده، بهویژه سطوح سیل و آببندهای ثانویه، سرنخهای حیاتی در مورد مکانیزم خرابی ارائه میدهد. یک بررسی روشمند کلیدی است.
نشانههای رایج خرابی و علل احتمالی:
- رد سایش سنگین و یکنواخت روی هر دو سطح:
- ظاهر: سطوح به طور قابل توجهی ساییده شدهاند اما به طور یکنواخت در سراسر مسیر تماس. سایش ممکن است فراتر از باند تماس معمولی گسترش یافته باشد.
- علل احتمالی: سایش عادی (سیل به سادگی به پایان عمر طبیعی خود رسیده است – کمتر برای خرابیهای زودهنگام رایج است). مواد ساینده (اگر سایش سریع و همراه با خراشیدگی/شیار باشد، احتمالاً مواد ساینده ریز در سیال فرآیندی یا فلاش وجود دارد). روانکاری ضعیف (آببندی سیالات با روانکنندگی کم بدون طراحی مناسب یا مواد مناسب). فشار بیش از حد (کارکرد بسیار بالاتر از درجه فشار سیل میتواند باعث بارگذاری بیش از حد سطح و سایش شود).
- رد سایش ناهموار / سایش در یک طرف:
- ظاهر: الگوی سایش به طور قابل مشاهدهای در یک طرف محیط سطح سنگینتر از طرف دیگر است.
- علل احتمالی: ناهمراستایی (ناهمراستایی شفت به محرک، ناهمراستایی داخلی پمپ (شفت خمیده، سطح محفظه سیل غیر عمود، سوراخ غیر هممرکز)، یا گلند به طور نامناسب پیچ شده که باعث لرزش سطح میشود). لرزش (سطوح بالای لرزش باعث عملکرد ناهموار سطوح میشود). انحراف شفت (کارکرد دور از BEP باعث انحراف شفت و بارگذاری ناهموار سطح میشود).
- سطوح لبپریده یا شکسته (بهویژه سطوح سخت مانند SiC، TC، سرامیک):
- ظاهر: لبهها یا بخشهایی از سطح(های) سیل به صورت فیزیکی شکسته یا لبپریده شدهاند. اغلب در لبه ID یا OD رخ میدهد.
- علل احتمالی: آسیب هنگام جابجایی (افتادن یا برخورد نادرست در حین نگهداری یا نصب). شوک مکانیکی (ناشی از لرزش شدید، حرکت شفت، فروپاشی کاویتاسیون در نزدیکی سیل، یا جهشهای فشار (مانند ضربه قوچ)). تماس سطح (تماس سخت به دلیل ناهمراستایی شدید یا از دست دادن فیلم سیال). جامدات (گیر کردن ذرات جامد بزرگ بین سطوح). مونتاژ نامناسب (کج شدن سیت ثابت در گلند، گیر کردن پینهای محرک).
- ترکهای حرارتی (Heat Checking / Thermal Cracking):
- ظاهر: ترکهای شعاعی ریز که از مسیر تماس روی سطح(های) سیل منشأ میگیرند، اغلب روی مواد سختتر دیده میشوند. میتواند شبیه الگوی “تار عنکبوت” باشد.
- علل احتمالی: گرمای بیش از حد (خنککاری ناکافی، قطع فلاش، کارکرد بالاتر از حد دما). کارکرد خشک (از دست دادن کامل فیلم سیال روانکننده، باعث اصطکاک شدید و شوک حرارتی میشود). تبخیر ناگهانی (Flashing) (تبخیر متناوب فیلم سیال به دلیل حاشیه فشار بخار ناکافی). سیال با روانکنندگی ضعیف (استفاده از مواد سطحی یا طراحی سیل نامناسب برای سیال). بار بیش از حد سطح (فشردگی بیش از حد یا کارکرد بالاتر از حد فشار).
- شیاردار شدن / خراشیدگی (Grooving / Scoring):
- ظاهر: خراشها یا شیارهای متحدالمرکز که در مسیر تماس روی سطح(های) سیل بریده شدهاند.
- علل احتمالی: مواد ساینده (ذرات سخت در سیال فرآیندی که در سطح نرمتر (اغلب کربن) فرو رفته و سطح سختتر را ماشینکاری میکنند، یا بین دو سطح سخت کشیده میشوند. سیستم فلاش (مثلاً کارایی جداکننده سیکلونی) را بررسی کنید). رسوبات سخت (محصول کریستالیزه یا کک شده که ذرات سختی را در سطوح تشکیل میدهد).
- تاول زدن / حفرهدار شدن (Blistering / Pitting) (معمولاً روی سطوح کربنی):
- ظاهر: حفرههای کوچک یا تاولهای برجسته روی سطح کربنی.
- علل احتمالی: حمله شیمیایی (سیال از نظر شیمیایی نسبت به گرید کربن مورد استفاده تهاجمی است). تبخیر ناگهانی/کاویتاسیون سیال (فروپاشی حبابهای بخار در سطح میتواند به طور فیزیکی به مواد آسیب برساند). جذب هیدروکربن (برخی هیدروکربنها میتوانند توسط کربن جذب شده و هنگام تغییر دما یا فشار منجر به تاول زدن شوند).
- رسوبات / کک شدن / تجمع محصول (Deposits / Coking / Product Build-up):
- ظاهر: تجمع قابل مشاهده مواد جامد روی سطوح (بهویژه سمت اتمسفری)، اطراف فنرها، بلوزها یا زیر آببندهای ثانویه. میتواند سخت (کک، کریستال) یا نرم/چسبناک (پلیمرها، لجن) باشد.
- علل احتمالی: اکسیداسیون/کک شدن (هیدروکربنها در معرض گرما و هوا در سمت اتمسفری قرار میگیرند. از کوئنچ Plan 62 استفاده کنید). کریستالیزاسیون (جامد شدن محصول هنگام خنک شدن یا تبخیر حلال پس از نشت به اتمسفر. از کوئنچ Plan 62 استفاده کنید). پلیمریزاسیون (واکنش سیال (اغلب با هوا یا گرما) برای تشکیل پلیمرها). سیال کثیف (تهنشین شدن جامدات در مناطق کم سرعت سیل یا محفظه).
- پیامد: میتواند منجر به سایش سطح (اگر ساینده باشد)، گیر کردن سیلهای پوشر یا بلوزها، و جلوگیری از تماس سطح شود.
- آسیب آببند ثانویه (اورینگها، گُوِهها، بلوزها):
- ظاهر: بریدگی، زدگی، اکستروژن، تورم، سخت شدن، ترک خوردن، تاول زدن، حمله شیمیایی، تغییر شکل دائمی (Compression Set)، سایش فرتینگ (روی شفت/غلاف زیر اورینگهای دینامیکی).
- علل احتمالی: آسیب هنگام نصب (بریده شدن روی لبههای تیز، پیچ خوردن یا گیر کردن در حین مونتاژ). ناسازگاری شیمیایی (الاستومر در برابر سیال فرآیندی یا مواد شیمیایی تمیزکننده مقاوم نیست). دمای بیش از حد (الاستومر از حد دمای خود فراتر رفته و باعث سخت شدن، ترک خوردن یا اکستروژن میشود). اکستروژن (ترکیبی از فشار بالا و دمای بالا، یا شکاف (Gap) بیش از حد). فرتینگ (سیلهای پوشر) (حرکت میکرو اورینگ دینامیکی در برابر شفت/غلاف، که اغلب توسط لرزش یا جامدات تشدید میشود). خرابی بلوز (خوردگی، ترک خستگی (لرزش، سیکلهای فشار)، گرفتگی).
- آسیب فنر/سختافزار:
- ظاهر: فنرهای شکسته، فنرها/سختافزار خورده شده، فنرهای مسدود شده.
- علل احتمالی: خوردگی (مواد با سیال فرآیندی سازگار نیست). خستگی (لرزش بالا یا استارت/استاپهای مکرر). گرفتگی (تجمع جامدات مانع عملکرد صحیح فنر میشود).
بررسی سیستماتیک، که اغلب با کمک بزرگنمایی و نور خوب انجام میشود، همراه با دانش طراحی و مواد سیل، به عیبیاب اجازه میدهد تا توالی احتمالی رویدادهای منجر به خرابی را استنباط کند. مستندسازی این یافتهها با عکس بسیار توصیه میشود.
جدول ۲: علائم رایج خرابی سیل و علل ریشهای بالقوه
علامت مشاهده شده | علت(های) ریشهای بالقوه | نواحی کلیدی برای بررسی |
---|---|---|
نشتی شدید قابل مشاهده | آسیب سطح (لبپریده، ترکخورده، ترک حرارتی، فرسوده)، خرابی آببند ثانویه (بریده، اکسترود شده، سخت شده)، گیر کردن (جامدات، رسوبات)، از دست دادن بار سطح (فنر شکسته، فشردگی ناکافی)، ناهمراستایی، لرزش، نصب نادرست. | اجزای سیل خراب (سطوح، الاستومرها، فنرها)، همراستایی پمپ، سطوح لرزش، رویه نصب، شرایط عملیاتی (فشار، دما)، عملکرد سیستم فلاش. |
عمر کوتاه سیل (خرابیهای مکرر) | مشکل اساسی سیستم برطرف نشده: ناهمراستایی، لرزش بالا، خرابی یاتاقان، انحراف شفت (عملکرد دور از BEP)، کاویتاسیون، پلان فلاش نامناسب، انتخاب نادرست سیل/مواد، شیوههای نصب ضعیف، سیال ساینده/خورنده. | تمام جنبهها: وضعیت مکانیکی پمپ، نقطه عملیاتی، آنالیز سیال فرآیندی، مشخصات سیل، بررسیهای نصب، عملکرد سیستم پشتیبانی، تاریخچه نگهداری. |
عملکرد پر سر و صدا (جیغ، ترق تروق) | کارکرد خشک، تبخیر ناگهانی سیال، روانکاری ضعیف، آسیب سطح (لبپریدگی باعث ایجاد صدا میشود)، لرزش بیش از حد، پدیده چسبیدن-لغزیدن (اغلب با الاستومرها یا جفتهای سطح خاص). | روانکاری (خواص سیال، فلاش)، حاشیه فشار بخار (کنترل دما/فشار)، وضعیت سطح، آنالیز ارتعاشات، وضعیت/روانکاری الاستومر. |
گرمای بیش از حد (ناحیه سیل / خطوط فلاش) | خنککاری ناکافی (جریان کم فلاش، خنککننده مسدود، عدم وجود آب خنککننده)، کارکرد خشک، بار بیش از حد سطح (فشردگی بیش از حد، فشار بالا)، بالانس نادرست سیل، اصطکاک بالا (روانکاری ضعیف، مواد اشتباه)، مشکلات بازچرخشی داخلی. | عملکرد پلان فلاش (جریان، دما)، عملکرد سیستم خنککاری، فشار عملیاتی در مقابل درجه سیل، طراحی سیل (بالانس؟)، مواد سطح، لقیهای داخلی پمپ. |
گیر کردن سیل (“Hang-Up”) (پوشر یا بلوز) | تجمع جامدات (زبالههای فرآیندی، کریستالها، کک، پلیمرها) که حرکت محوری آببند ثانویه دینامیکی یا بلوز را محدود میکند. | آنالیز سیال فرآیندی (جامدات، تمایل به کریستالیزاسیون/پلیمریزاسیون)، اثربخشی فلاش، کاربرد کوئنچ (Plan 62)، انتخاب طراحی سیل (غیرپوشر را در نظر بگیرید). |
شفت/غلاف آسیبدیده زیر سیل | سایش فرتینگ (حرکت اورینگ دینامیکی سیل پوشر، تشدید شده توسط لرزش/جامدات)، آسیب پیچ تنظیم (سفت کردن بیش از حد، نوع/محل نادرست). | سطوح لرزش، وجود جامدات، در صورت تکرار فرتینگ، سیل بلوز را در نظر بگیرید، رویههای سفت کردن/گشتاور پیچ تنظیم را بازبینی کنید. |
متدولوژی تحلیل علل ریشهای (RCA)
یافتن علت فوری خرابی (مانند “سطوح فرسوده”) تنها قدم اول است. بهبود واقعی از شناسایی علت ریشهای – دلیل بنیادی وقوع خرابی – حاصل میشود. متدولوژیهایی مانند “5 چرا” (5 Whys) یا نمودارهای استخوان ماهی (ایشیکاوا) میتوانند مفید باشند.
مثال با استفاده از 5 چرا:
- چرا سیل خراب شد؟ نشتی بیش از حد.
- چرا نشتی بیش از حد وجود داشت؟ سطوح سیل داخلی به شدت شیاردار شده بودند.
- چرا سطوح شیاردار شده بودند؟ ذرات ساینده در سیال فرآیندی بین سطوح گیر کرده بودند.
- چرا ذرات ساینده به سطوح میرسیدند؟ جداکننده سیکلونی Plan 31 در خط فلاش آنها را به طور مؤثر حذف نمیکرد.
- چرا جداکننده سیکلونی ناکارآمد بود؟ با جامدات تهنشین شده تا حدی مسدود شده بود که کارایی آن را کاهش داده بود و اختلاف فشار دو سر آن برای عملکرد مناسب بسیار کم بود.
علت ریشهای: نگهداری ناکافی سیستم پشتیبانی سیل (جداکننده مسدود) و احتمالاً طراحی/عملکرد نادرست سیستم (اختلاف فشار ناکافی).
اقدامات اصلاحی: اجرای برنامه تمیزکاری منظم برای جداکننده، تأیید اندازه صحیح اوریفیس و فشار عملیاتی پمپ برای اطمینان از اختلاف فشار کافی برای جداکننده. در صورت شدید بودن مواد ساینده، پلان فلاش جایگزین (مانند فلاش تمیز Plan 32) را در نظر بگیرید.
RCA نیازمند جمعآوری دادههای جامع است:
- اجزای سیل خراب شده (با دقت جابجا کنید، کیسهها را برچسب بزنید)
- گزارشهای دادههای عملیاتی (فشار، دما، جریان، لرزش) منتهی به خرابی
- سوابق نگهداری (خرابیهای قبلی، جزئیات نصب، نگهداری سیستم فلاش)
- شرایط فرآیندی (خواص سیال، وجود جامدات، پتانسیل شرایط نامطلوب)
- اطلاعات وضعیت پمپ (سوابق همراستایی، وضعیت یاتاقان، اندازهگیریهای لنگی)
تحلیل جمعی این دادهها، که اغلب شامل یک تیم چند تخصصی (نگهداری، عملیات، مهندسی) است، منجر به تشخیص دقیقتر و اقدامات اصلاحی مؤثرتر میشود.
اقدامات اصلاحی و یادگیری از خرابیها
پس از شناسایی علت ریشهای، اقدامات اصلاحی مناسب را اجرا کنید. این ممکن است شامل موارد زیر باشد:
- تغییرات رویهای: بهبود تکنیکهای نصب، بازنگری رویههای راهاندازی/توقف، اجرای پروتکلهای تمیزکاری بهتر.
- تعدیل استراتژی نگهداری: افزایش فرکانس بازرسی، افزودن بررسیهای PdM خاص (مانند آنالیز ارتعاشات مکررتر)، بهبود PMهای سیستم فلاش.
- تغییرات عملیاتی: تنظیم نقطه عملیاتی پمپ نزدیکتر به BEP، کنترل جهشهای فشار سیستم.
- ارتقاء طراحی/مواد: انتخاب طراحی سیل قویتر (مانند کارتریجی، بلوز، بالانس)، ارتقاء مواد سطح یا الاستومر برای مقاومت بهتر شیمیایی/سایندگی/دمایی، اصلاح پمپ (مانند محفظه سیل با سوراخ بزرگتر)، اجرا یا ارتقاء پلان فلاش API.
به طور حیاتی، کل فرآیند را مستند کنید: حالت خرابی، یافتههای RCA، اقدامات اصلاحی انجام شده و عملکرد بعدی سیل. این یک پایگاه دانش ایجاد میکند که از تکرار اشتباهات جلوگیری کرده و بهبود مستمر در قابلیت اطمینان سیل در سراسر تأسیسات را هدایت میکند. به اشتراک گذاشتن این درسهای آموخته شده بین کارکنان نگهداری و مهندسان حیاتی است.
عیبیابی خرابیهای سیل مکانیکی یک فرآیند کارآگاهی است. با بررسی دقیق شواهد (قطعات خراب شده) و در نظر گرفتن زمینه (شرایط عملیاتی، تاریخچه نگهداری)، میتوان علل اساسی را کشف کرد و به راهحلهای هدفمندی رسید که واقعاً عمر سیل را افزایش داده و قابلیت اطمینان تجهیزات را بهبود میبخشد.
بخش ۶: مباحث پیشرفته و روندهای آینده
در حالی که تسلط بر اصول انتخاب، نصب، بهرهبرداری و نگهداری سیل، پایه و اساس قابلیت اطمینان را فراهم میکند، چندین موضوع پیشرفته و روندهای نوظهور فرصتهای بیشتری برای بهینهسازی و افزایش عملکرد ارائه میدهند.
ملاحظات انتخاب سیل برای کاربردهای چالشبرانگیز
پیکربندیهای استاندارد سیل ممکن است هنگام مواجهه با شرایط فرآیندی بهویژه سخت، ناکافی باشند. رسیدگی به این چالشها اغلب نیازمند طراحیهای سیل تخصصی، مواد یا سیستمهای پشتیبانی است.
- دماهای بالا: فراتر از محدودیتهای الاستومرهای استاندارد (حدود 200 درجه سانتیگراد / 400 درجه فارنهایت)، آببندی ثانویه به موادی مانند گرافیت انعطافپذیر (مانند Grafoil®)، PTFE (با محدودیتهای دمایی و نگرانیهای خزش) یا بلوزهای فلزی متکی است. سیلهای بلوز فلزی الاستومرها را به طور کامل از ناحیه آببندی دینامیکی حذف میکنند و هنگامی که از آلیاژهای مناسب (مانند Inconel®، Alloy 276) ساخته شوند، میتوانند دماهای بیش از 400 درجه سانتیگراد / 750 درجه فارنهایت را تحمل کنند. انتخاب مواد سطح نیز حیاتی میشود و مواد پایداری مانند کاربید سیلیکون یا کاربید تنگستن، بالقوه با گریدهای تخصصی، ترجیح داده میشوند. خنککاری مؤثر از طریق پلانهای API (مانند Plan 21, 23, 32 با فلاش خنک شده، Plan 53B/C/54 با خنککنندهها) اغلب ضروری است.
- فشارهای بالا: سیلهای غیربالانس معمولاً به حدود 10-20 بار (150-300 psi)، بسته به اندازه و سرعت، محدود میشوند. برای فشارهای بالاتر، سیلهای بالانس برای کاهش بارگذاری سطح و تولید گرما مورد نیاز هستند. درجه بالانس میتواند متناسب با نیاز تنظیم شود. سیلهای دوبل تحت فشار (چیدمان 3 / Plan 53 یا 54) نیز میتوانند فشارهای بالای فرآیندی را با انتقال اختلاف فشار اصلی به سیستم سیال مانع تحمل کنند، که به سیل داخلی اجازه میدهد در اختلاف فشار کمتری کار کند. استحکام مواد و مقاومت در برابر تغییر شکل تحت فشار برای همه اجزا مهم میشود.
- دوغابهای ساینده (Abrasive Slurries): مقابله با غلظتهای قابل توجه ذرات سخت و ساینده نیازمند یک رویکرد چند وجهی است.
- سطوح سخت: استفاده از ترکیبات مواد سطح بسیار سخت مانند کاربید سیلیکون در مقابل کاربید سیلیکون (SiC/SiC) یا کاربید تنگستن در مقابل کاربید تنگستن (TC/TC) مقاومت در برابر سایش را به حداکثر میرساند. SiC سینتر شده عموماً عملکرد بهتری در دوغابهای سنگین نسبت به SiC با پیوند واکنشی ارائه میدهد.
- کنترلهای محیطی: جداسازی سیل از دوغاب اغلب مؤثرترین استراتژی است. این شامل استفاده از فلاش تمیز خارجی (Plan 32) یا به کارگیری سیلهای دوبل تحت فشار (Plan 53/54) با سیال مانع تمیز است که سطوح را روانکاری میکند. اگر از سیال فرآیندی بازچرخشی استفاده میشود (Plan 11/13)، یک جداکننده سیکلونی بسیار مؤثر (Plan 31) مورد نیاز است، اما اثربخشی آن به اندازه/چگالی ذرات و اختلاف فشار کافی بستگی دارد.
- طراحی سیل: ویژگیهایی مانند لقیهای داخلی بزرگ، طراحیهای فنر غیر مسدود شونده و طراحیهای بلوز قوی (در صورت کاربرد) میتوانند تحمل نسبت به جامدات را بهبود بخشند. گاهی اوقات، “سیلهای دوغاب” تخصصی با فنرهای محافظت شده و هندسههای سطح خاص استفاده میشود.
- سیالات چسبناک یا پلیمریزه شونده: سیالاتی که غلیظ میشوند، جامد میشوند یا پلیمریزه میشوند میتوانند مکانیزمهای سیل را مسدود کرده و در روانکاری سطح اختلال ایجاد کنند.
- کنترل دما: گرم کردن محفظه سیل (مانند گلند با ژاکت بخار) میتواند سیالات چسبناک را روان نگه دارد. برعکس، ممکن است برای جلوگیری از پلیمریزاسیون ناشی از گرما، نیاز به خنککاری باشد.
- فلاش/کوئنچ: تزریق فلاش تمیز و سازگار (Plan 32) میتواند سیل را جدا کند. کوئنچ بخار یا حلال داغ (Plan 62) در سمت اتمسفری میتواند از تجمع جلوگیری کند.
- طراحی سیل: سیلهای غیرپوشر (بلوز) کمتر مستعد گیر کردن ناشی از تجمع جامدات روی شفت/غلاف هستند. طراحیهایی با ویژگیهای باز و غیر مسدود شونده ترجیح داده میشوند. سیلهای دوبل (Plan 53/54) جداسازی را فراهم میکنند.
- شرایط کارکرد خشک (بالقوه یا واقعی): شرایطی که پمپ ممکن است به طور موقت مکش خود را از دست داده یا خشک کار کند (مانند تخلیه تانکر، فرآیندهای دستهای) برای سیلهای معمولی که به سیال فرآیندی برای روانکاری متکی هستند، فاجعهبار است.
- سیلهای دوبل: سیلهای دوبل تحت فشار (Plan 53/54) روانکاری خود را از طریق سیال مانع تأمین میکنند و به آنها اجازه میدهد تا از دست دادن سیال فرآیندی را تحمل کنند.
- سیلهای تکی تخصصی: برخی طراحیهای سیل تکی شامل ویژگیهایی برای تحمل محدود کارکرد خشک هستند، مانند ترکیبات مواد سطح خاص (مانند پوششهای الماسی) یا هندسههایی که برای ایجاد مقداری بالابری حتی با حداقل سیال طراحی شدهاند، اما اینها اغلب محدودیتهایی دارند.
- ابزار دقیق: سنسورهای سطح یا سوئیچهای جریان میتوانند از دست دادن پرایم را تشخیص داده و قبل از آسیب دیدن سیل، پمپ را خاموش کنند.
- الزامات انتشار صفر: برای سیالات بسیار خطرناک یا سمی که در آنها نشتی کاملاً حداقلی مجاز است، سیلهای دوبل تحت فشار (چیدمان 3 / Plan 53 یا 54) راهحل استاندارد هستند و بالاترین سطح مهار را فراهم میکنند. سیلهای روانکاری شده با گاز (به زیر مراجعه کنید) نیز انتشار نزدیک به صفر را ارائه میدهند. سیلهای تاندوم (چیدمان 2 / Plan 52) مهار ثانویه را فراهم میکنند اما همچنان اجازه نشتی سیل اولیه به سیستم بافر را میدهند.
سیلهای روانکاری شده با گاز (سیلهای گاز خشک)
یک دسته متمایز از سیلهای مکانیکی، که اغلب سیلهای گاز خشک (DGS) یا سیلهای روانکاری شده با گاز نامیده میشوند، با یک فیلم گازی بین سطوح به جای فیلم مایع کار میکنند. آنها بیشتر در کمپرسورهای گاز استفاده میشوند اما کاربرد فزایندهای در پمپها پیدا میکنند، بهویژه در پیکربندیهای چیدمان 3 (دوبل تحت فشار) که در آن یک گاز بیاثر تحت فشار (مانند نیتروژن) به عنوان محیط مانع عمل میکند.
- اصل عملکرد: این سیلها دارای شیارهای با مهندسی دقیق (شیارهای هیدرودینامیکی یا مارپیچی) روی یکی از سطوح سیل هستند. با چرخش شفت، این شیارها گاز را به سمت داخل پمپ کرده و فشار فیلم گازی بسیار پایداری ایجاد میکنند که سطوح را با فاصله چند میکرومتر (معمولاً 3-5 میکرومتر) از هم جدا میکند. این یک سیل بدون تماس ایجاد میکند.
- مزایا:
- انتشار فرآیندی نزدیک به صفر: هنگام استفاده در چیدمان سیل دوبل با گاز مانع، نشتی سیال فرآیندی به اتمسفر عملاً حذف میشود. نشتی گاز مانع بسیار کم است.
- اصطکاک و مصرف برق کم: عملکرد بدون تماس منجر به اصطکاک و تولید گرمای قابل توجهی کمتر در مقایسه با سیلهای روانکاری شده با مایع میشود.
- عمر طولانی: عدم وجود تماس سطح منجر به نرخ سایش بسیار پایین و عمر عملیاتی بالقوه بسیار طولانی میشود که عمدتاً توسط تخریب آببند ثانویه یا مشکلات آلودگی محدود میشود.
- تحمل کارکرد خشک: از آنجا که برای کار با گاز طراحی شدهاند، از دست دادن موقت مایع فرآیندی کمتر مضر است (در چیدمانهای سیل گاز دوبل).
- معایب:
- نیاز به تأمین گاز تمیز: گاز مانع باید تمیز، خشک و با فشار صحیح تأمین شود. آلودگی (مایع یا ذرات) میتواند باعث آسیب سطح یا ناپایداری شود. نیاز به یک پنل تأمین گاز پیچیده (شبیه به API Plan 74) دارد.
- هزینه اولیه بالاتر: سیلهای گازی و سیستمهای پشتیبانی آنها عموماً گرانتر از سیلهای مایع معمولی هستند.
- حساسیت به فشار معکوس: برخی طراحیها به معکوس شدن فشار حساس هستند.
- استفاده محدود به عنوان سیل تکی در مایعات: در حالی که امکانپذیر است، استفاده مستقیم از سیلهای گازی در برابر یک فرآیند مایع اغلب نیاز به کنترل دقیق فشار دارد و در صورت تبخیر ناگهانی مایع یا حاوی جامدات بودن آن، چالشهایی را ایجاد میکند. چیدمانهای سیل گاز دوبل در پمپها رایجتر هستند.
- کاربردها: عمدتاً برای خدمات حیاتی که نیاز به انتشار نزدیک به صفر دارند (VOCها، سیالات خطرناک)، کاربردهایی که آلودگی فرآیند توسط سیال مانع مایع غیرقابل قبول است، یا جایی که عمر بسیار طولانی سیل مورد نظر است، استفاده میشود.
فناوری سیل گاز نشاندهنده پیشرفت قابل توجهی برای کاربردهای خاص پرتقاضا است که در صورت کاربرد و پشتیبانی صحیح، مزایای زیستمحیطی و قابلیت اطمینان را ارائه میدهد.
نقش استانداردسازی (API 682)
استاندارد موسسه نفت آمریکا API 682: پمپها—سیستمهای آببندی شفت برای پمپهای سانتریفیوژ و دوار، به استاندارد جهانی بالفعل برای سیلهای مکانیکی در خدمات حیاتی پالایشگاهی، پتروشیمی و فرآوری گاز تبدیل شده است، اما اصول آن به طور گسترده در صنایع دیگر نیز به کار گرفته میشود.
- هدف: API 682 با هدف بهبود ایمنی و قابلیت اطمینان سیلهای مکانیکی در کاربردهای سخت، با ایجاد الزامات حداقل برای طراحی سیل، مواد، تست صلاحیت، انتخاب، کنترلهای محیطی (پلانهای API) و مستندسازی است.
- ویژگیهای کلیدی:
- دستهبندی: دستهبندیهای سیل را بر اساس ویژگیهای طراحی و شدت خدمات مورد نظر تعریف میکند.
- استانداردسازی: استفاده از طراحیهای سیل کارتریجی استاندارد را ترویج میکند و قابلیت تعویضپذیری و انتخاب را بهبود میبخشد.
- انتخابهای پیشفرض: انواع سیل پیشفرض (مانند نوع A, B, C) و چیدمانها (تکی، دوبل بدون فشار، دوبل تحت فشار) را بر اساس خواص سیال و شرایط عملیاتی ارائه میدهد.
- پلانهای API: سیستمهای مختلف کنترل محیطی سیل (پلانهای فلاش، بافر، مانع) را استاندارد و جزئیات میدهد.
- تست صلاحیت: نیاز به تست دقیق طراحیهای سیل تحت شرایط مشخص برای اثبات قابلیتهای عملکردی دارد.
- تأکید بر قابلیت اطمینان: عمر حداقل سیل سه سال (25,000 ساعت) خدمات بدون وقفه را هدف قرار میدهد.
- تأثیر: پایبندی به API 682 عموماً منجر به انتخاب راهحلهای آببندی قویتر و قابل اطمینانتر (اغلب سیلهای کارتریجی، مواد خاص، سیستمهای پشتیبانی به خوبی تعریف شده) میشود و به طور قابل توجهی به بهبود MTBF در خدمات حیاتی کمک میکند. اگرچه در ابتدا گرانتر است، تمرکز بر هزینه چرخه عمر اغلب سرمایهگذاری را از طریق کاهش خرابیها و توقفها توجیه میکند. درک اصول API 682 حتی برای کاربردهایی که به طور دقیق تحت پوشش استاندارد نیستند نیز مفید است، زیرا بهترین شیوههای صنعت را نشان میدهد.
اینترنت اشیاء (IoT) و تحلیلهای پیشبینانه در پایش سیل
ادغام سنسورها، قابلیت اتصال (اینترنت اشیاء – IoT) و تحلیل دادههای پیشرفته، در حال تغییر پایش و نگهداری سیل مکانیکی است.
- حسگری پیشرفته: فراتر از سنسورهای سنتی فشار، دما و سطح روی سیستمهای پشتیبانی، سنسورها میتوانند نزدیکتر به یا درون خود سیل برای پایش پارامترهایی مانند:
- دمای سطح سیل
- لرزش مستقیماً در گلند
- انتشارات آکوستیک (تشخیص اصطکاک، ضربهها، تبخیر ناگهانی)
- نرخ نشتی (با استفاده از آشکارسازهای تخصصی)
- وضعیت سیال مانع/بافر (مانند هدایت الکتریکی برای آلودگی)
- قابلیت اتصال و جمعآوری دادهها: پلتفرمهای IoT امکان جمعآوری مداوم و از راه دور دادهها از این سنسورها را فراهم کرده و آن را به سرورهای مبتنی بر ابر یا محلی منتقل میکنند.
- تحلیلهای پیشبینانه: الگوریتمهای یادگیری ماشین دادههای سنسور ورودی را به همراه دادههای تاریخی و پارامترهای عملیاتی تحلیل میکنند تا:
- انحرافات جزئی از الگوهای عملیاتی عادی را شناسایی کنند.
- علائم هشدار دهنده اولیه خرابیهای در حال توسعه را تشخیص دهند (مانند افزایش جزئی روند دمای سطح قبل از گرم شدن بیش از حد).
- پارامترهای متعدد را برای تشخیص حالت خرابی محتمل مرتبط کنند.
- عمر مفید باقیمانده (RUL) سیل را پیشبینی کنند.
- هنگامی که نگهداری مورد نیاز است، هشدارها و دستور کارهای خودکار را فعال کنند.
- مزایا: این رویکرد فراتر از نگهداری برنامهریزی شده یا مبتنی بر وضعیت حرکت کرده و به سمت نگهداری واقعاً پیشبینانه میرود و امکان موارد زیر را فراهم میکند:
- تشخیص زودهنگامتر خرابیهای بالقوه، به حداقل رساندن آسیبهای متعاقب.
- تشخیص دقیقتر علل ریشهای.
- برنامهریزی بهینه نگهداری بر اساس نیاز واقعی.
- کاهش توقف برنامهریزی نشده و هزینههای مرتبط.
- درک بهتر رفتار سیل تحت شرایط عملیاتی مختلف.
اگرچه هنوز در حال تکامل است، کاربرد IoT و تحلیلهای پیشبینانه نویدبخش افزایش بیشتر قابلیت اطمینان سیل مکانیکی و تبدیل شیوههای نگهداری از واکنشی یا پیشگیرانه به پیشبینانه و پیشگیرانه است.
نتیجهگیری: تلفیق بهترین شیوهها برای عمر بهینه سیل
سیلهای مکانیکی، اگرچه اجزای به ظاهر سادهای هستند، بر اساس تعادل ظریفی از نیروها عمل میکنند و برای بقای خود به یک فیلم سیال میکروسکوپی متکی هستند. دستیابی به عمر خدمات قابل اعتماد سه سال به بالا، مسئله شانس نیست، بلکه نتیجه یک رویکرد سیستماتیک و جامع است که به هر مرحله از چرخه عمر سیل میپردازد.
نکات کلیدی برای به حداکثر رساندن قابلیت اطمینان سیل:
- انتخاب صحیح، بنیادی است: نوع سیل مناسب (پوشر/بلوز، بالانس/غیربالانس)، چیدمان (تکی، دوبل، تاندوم)، مواد (سطوح، الاستومرها، سختافزار) و پلان کنترل محیطی (پلان API) را بر اساس درک کامل شرایط عملیاتی (فشار، دما، سرعت) و ویژگیهای سیال فرآیندی (روانکنندگی، مواد ساینده، خورندگی، فشار بخار) انتخاب کنید. از استانداردهایی مانند API 682 برای راهنمایی در کاربردهای حیاتی استفاده کنید.
- وضعیت پمپ بسیار مهم است: یک سیل نمیتواند در پمپی با سلامت مکانیکی ضعیف زنده بماند. از همراستایی دقیق پمپ/محرک، حداقل لنگی و بازی محوری شفت، یاتاقانهای سالم و کارکرد نزدیک به نقطه بهترین راندمان (BEP) پمپ اطمینان حاصل کنید. قبل از نصب سیل جدید، مشکلات پمپ را برطرف کنید.
- نصب دقیق حیاتی است: نصب را به عنوان یک کار دقیق در نظر بگیرید. بررسیهای پیش از نصب را به طور جدی انجام دهید. سیلها را با دقت جابجا کنید، تمیزی مطلق را حفظ کنید، از روانکاری صحیح استفاده کنید، رویههای سازنده را دقیقاً دنبال کنید (بهویژه برای مقادیر گشتاور و برداشتن گیره تنظیم برای کارتریجها) و از همراستایی مناسب گلند اطمینان حاصل کنید. سیلهای کارتریجی خطاهای نصب را به طور قابل توجهی کاهش میدهند.
- بهرهبرداری و پایش مؤثر: پمپ را در محدوده طراحی آن به کار بگیرید. از رویههای صحیح ونت و راهاندازی برای جلوگیری از کارکرد خشک اطمینان حاصل کنید. پارامترهای عملیاتی (نشتی، صدا، دما، لرزش) و شرایط سیستم پشتیبانی سیل (سطح، فشار، جریان) را به دقت پایش کنید. در صورت امکان از فناوریهای نگهداری پیشبینانه استفاده کنید.
- محیط را حفظ کنید: سیستمهای پشتیبانی سیل (پلانهای API) لوازم جانبی اختیاری نیستند؛ آنها برای بقای سیل در شرایط چالشبرانگیز حیاتی هستند. آنها را با دقت نگهداری کنید – از جریان/فشار/دمای صحیح اطمینان حاصل کنید، سیالات را تمیز نگه دارید و از انسداد در خطوط، خنککنندهها و جداکنندهها جلوگیری کنید.
- از خرابیها بیاموزید: هنگامی که سیلها پیش از موعد خراب میشوند، تحلیل علل ریشهای (RCA) کامل انجام دهید. اجزای خراب شده را به دقت بررسی کنید، یافتهها را با دادههای عملیاتی و نگهداری مرتبط کنید، علت(های) بنیادی را شناسایی کنید و اقدامات اصلاحی مؤثر را اجرا کنید. درسهای آموخته شده را مستند کرده و به اشتراک بگذارید.
دستیابی به قابلیت اطمینان بلندمدت سیل مکانیکی نیازمند یک تغییر فرهنگی به سمت مدیریت پیشگیرانه، توجه به جزئیات، یادگیری مستمر و در نظر گرفتن سیل به عنوان بخشی از یک سیستم یکپارچه است. با سرمایهگذاری در انتخاب مناسب، تضمین سلامت تجهیزات، اتخاذ بهترین شیوهها برای نصب و نگهداری و پایش دقیق عملکرد، تأسیسات میتوانند به طور قابل توجهی خرابیهای سیل را کاهش دهند، توقف پرهزینه را به حداقل برسانند، ایمنی را افزایش دهند و کارایی کلی عملیاتی را بهبود بخشند. فناوری برای آببندی قابل اعتماد وجود دارد؛ کاربرد مداوم این اصول کلید باز کردن پتانسیل کامل آن است.
سلب مسئولیت: این مقاله اطلاعات عمومی و بهترین شیوهها را در مورد نگهداری سیل مکانیکی ارائه میدهد. کاربردهای خاص ممکن است الزامات منحصر به فردی داشته باشند. همیشه برای راهنمایی متناسب با وضعیت خاص خود، به مستندات سازنده تجهیزات، استانداردهای صنعتی مربوطه (مانند API 682) و پرسنل مهندسی واجد شرایط مراجعه کنید. هنگام کار با تجهیزات دوار و سیالات بالقوه خطرناک، باید همیشه اقدامات احتیاطی ایمنی رعایت شود.